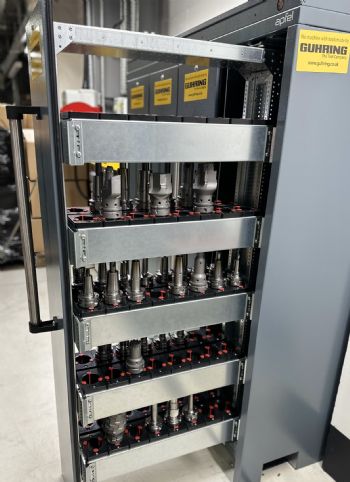
As a manufacturer four- and five-axis machining centres for the global market, Redditch-based
Heller UK is frequently involved in turnkey projects. One recent project for a manufacturer of electric vehicles (EVs) saw the company enlisting the support of the cutting tool experts from
Guhring Ltd, Birmingham, for a comprehensive package of cutting tools, tool holders, chucks and tool-vending technology.
The cutting tools for this project included a wide range of Guhring’s standard drills, taps and reamers that were selected and tested to minimise cycle times while achieving tight tolerances on diameter, position and roundness; and while standard products accounted for a significant amount the project’s tooling, it was the bespoke PCD combination tools that highlight the capabilities of Guhring UK as a one-stop solution provider with its ability to achieve ‘one shot’ plunging, short cycle times, and high levels of surface finish — and maintaining this over the life of the tool.
Chris Bush, Guhring UK’s national sales manager, said: “With a new project like this for the EV industry, the end user typically specifies a machine builder and cutting tool supplier; in this instance, Heller for the machines and Guhring for the tooling. In Germany, we have a large project engineering team with over 200 employees, so when we receive a CAD model of the customers’ component and the machine capabilities, we develop the cutting tools and machining strategies and, in this case with Heller, develop an optimised production solution.
“This particular project required many meetings to discuss the machining strategies and how we would develop the tooling to create a seamless solution from machine tool to cutting tool. Guhring has supplied everything from tool holder to the cutting-edge; and in conjunction with Heller, also established all the speeds, feeds and cutting strategies. We also visited Heller for the initial run-offs to ensure all the cutting data was optimised and the machining strategy worked well — and will follow the process through to end-user production.
“This EV project was the largest we have collaborated on in the UK; and in addition to the tools and tool holding, we are supplying the tool management vending solution, which can be linked to the customer’s ERP system.”
For this project, Heller delivered 22 machines, comprising 11 five-axis machines and 11 four-axis types — all built in the UK — along with all the custom hydraulic fixtures to hold the parts.