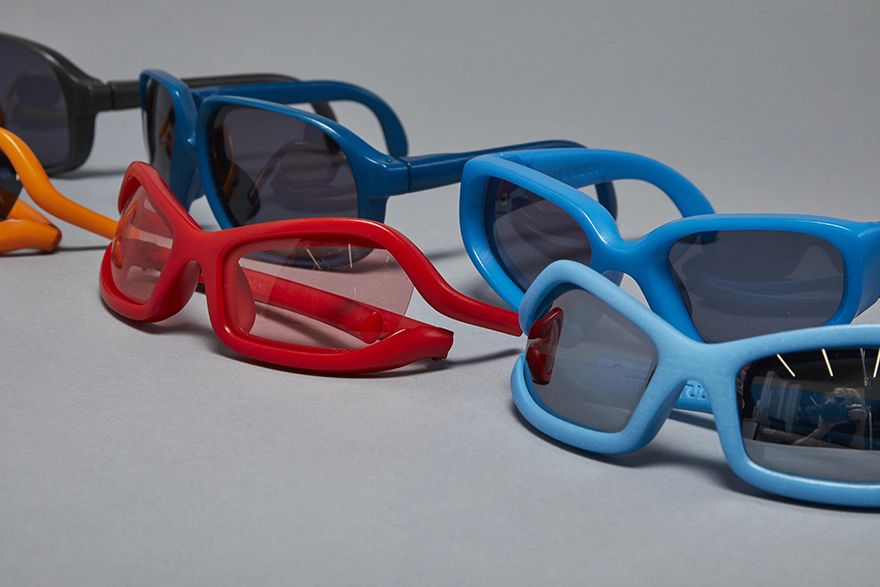
London-based
3D People, a leading provider of high-quality 3-D printed parts on demand, has expanded its colour dye finishing service. The company is focused on delivering the highest quality 3-D printed parts in the most efficient way possible for its customers whether they order a single part or many thousands in production batches.
Most recently, the team at 3D People has specifically turned its attention to expanding the range of high-quality finishes available to its customers. As of now, customers have the option to select any of 170 dye colours for their 3-D printed parts.
Felix Manley, co-founder of 3D People, said: “We believe that we are the only additive manufacturing (AM) service bureau in the UK that offers such a broad spectrum of colour options for products and parts. We know that coloured parts are not always a priority for many standard applications of AM, however, for many non-standard applications where colour is important, the choices are often limited to basic primary colours. Our new colour finishing service has the ability to match colours to the RAL colour system, ensuring precise colour consistency for industries or brands that require standardised colours.”
The increased colour palette available at 3D People makes it possible to select and create specific custom brand colours for parts, which can be subsequently stored for future orders, enabling consistent colour branding across all products and components that require it. Furthermore, these extensive colour dye options can be combined with 3D People’s other premium finish options, which include vibro polishing and automated vapour smoothing to achieve a smooth, high-end finish, enhancing the overall aesthetic and feel of the part, as well as improved part properties.
One customer that is taking full advantage of the full colour and advanced finishing options from 3D People is
Tides Studios, also based in London. Originally established as a sustainable design consultancy, Tides has maintained its commitment to sustainability throughout its transition into the eyewear industry. This was one of the key factors of working with 3D People, because everything that Tides produces — the glasses themselves as well as the cases and packaging — are all designed, manufactured and assembled in London.
Solid colour rangeBeyond geography, however, Tides works with companies that supply quality and colour options that work for its brand. Joseph Alpert, founder of Tides Studios, said: “Finding an AM partner with a solid colour range was a struggle. Most only had basic colours, and paint trials always cracked or flaked. Since 3D People rolled out its 170 standard colours, we have shifted all of our production to the company. Its durable dyes hold up great for eyewear, and the colour options are perfect for what we need. Plus, working with its team on non-standard colours has been a pleasure — 3D People really gets what we are looking for. Its vapour smoothing also makes the colours pop more than anything we have seen from other suppliers.”
From experience and intensive testing, the 3D People team has demonstrated that dyed AM parts offer flexibility without cracking, maintaining their colour integrity even when flexed or bent, thus avoiding the cracking or flaking that often occurs with a painted finish. Moreover, dyed parts also exhibit uniform and consistent colour coverage as well as enhanced durability with greater wear resistance when compared with paint finishes. This is because the dye colour process ensures that the dye penetrates into the top layers of the part rather than sitting on the surface, which prevents chipping or peeling.
Sasha Bruml, co-founder of 3D People, said: “Quality is central to our entire 3-D printing service offering from beginning to end, and the foundation of our reputation. We are listening to our customers and they are excited by these new colour options for finishing because it offers them extensive customisation opportunities with AM. In some cases, it is providing them with a competitive advantage when it comes to their customised and brand colour choices without having to outsource painting to a third party with the inevitable costs that brings.”
Colouring AM parts is proving to be a cost-effective solution because it eliminates the need for primers, multiple coats of paint, as well as post-painting treatments. Not only is it more sustainable, with reduced material and labour costs, but it also offers a more permanent, flexible and robust colour solution. The 3D People colour service is proving ideal for both prototypes and end-use parts, especially in applications where wear and aesthetics are crucial.
Mr Manley concluded: “This is just one small, but important, step forward for 3D People in achieving excellence in the finishing of 3-D printed parts. The future needs to look beyond the use of AM to make parts, and onto the ability to produce repeatable surface finishes which rival and are often superior to parts produced using conventional manufacturing processes.”