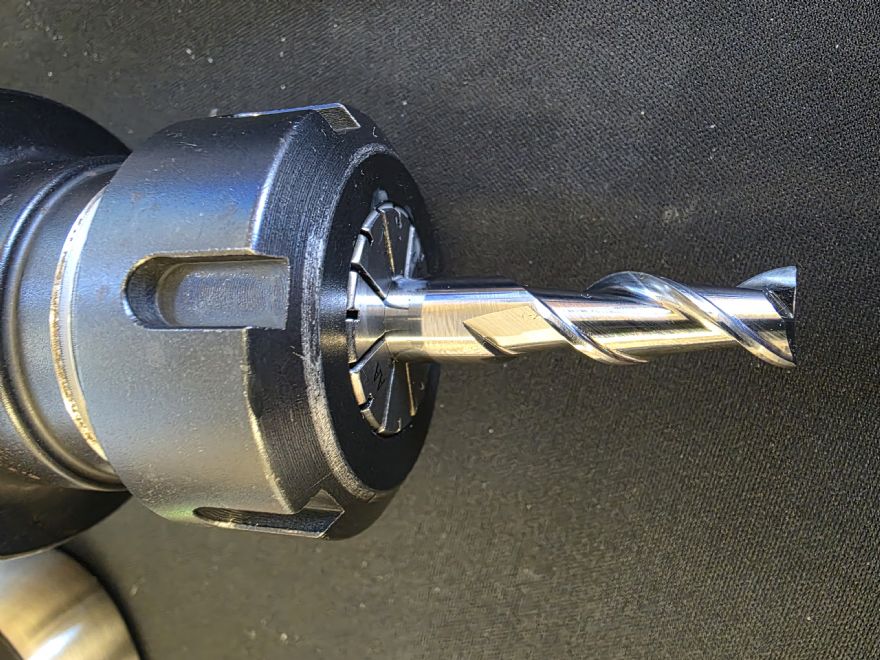
Oldbury-based
Narvik Developments Ltd, a mould, tool and pattern manufacturer, has said ‘speed is certainly of the essence’, with the company having a packed order book of customers from across the automotive, aerospace and general sub-contract markets.
Gavin Lee, the company’s works manager, said: “It is all about shifting metal, and the quicker you can get the job finished, the better. We are currently turning over jobs about every two months at the moment — and there is a lot of variety. Over the past 30 years, we have established a strong reputation for the remanufacture of press tools. The company has also made significant infrastructure investments to handle workpieces of up to 10 tonnes and has two machine shops running simultaneously on site; and with the pace we are working at, we need our suppliers to help us overcome any challenges as quickly as possible.”
One partnership that has become increasingly important to Narvik is with its metalworking, safety and MRO supplier,
MSC Industrial Supply Co UK. In 2022, MSC was supplying Narvik with consumables such as safety boots and ground flat stock, but the company is now a key tooling supplier for the company’s 11 metal-cutting machines.
Mr Lee said: “I have established a great working relationship with Mark Evans, MSC’s territory account manager, and I know that if I share a machining challenge with him, he will come back with the right tools to get the job done. Even if we are machining something really challenging, MSC will put me in contact with the right supplier to get the job done.”
MSC EdgeNarvik’s diverse tooling challenges proved particularly interesting to MSC, and the company quickly became a test site for the launch of MSC Edge, a new brand of multi-purpose cutting tool designed by MSC engineers. Over the course of several weeks, MSC’s engineering team conducted a broad range of trials across different materials and tool paths to help find the ideal tooling solution for Narvik Developments. The project also proved a critical data-gathering exercise ahead of the launch of MSC Edge.
Following the completion of the trials, Narvik was supplied with a series of solid-carbide hole making and milling tools. Mr Lee said: “We have been completing a mix of profiling and finishing work on aerospace aluminium, which is quite an abrasive material. The tools have been in use for several weeks and have kept their edge. Moreover, we put them straight into the machine and it was pretty much ‘plug and play’; we didn’t need to change the feeds or speeds, and it was a case of putting them in the magazine and pressing go.”
Mr Evans concluded: “The work that Gavin and Narvik are undertaking is reflective of the broader changes we have seen across the precision engineering sector, namely a move towards more contract work across a variety of industry sectors; and while diversification increases the number of potential opportunities, it can very easily also increase tooling costs. Helping engineers like Gavin and his team rationalise their tooling was a key element in the development of MSC Edge.”