Key Precision has carved out a remarkable niche since its inception. As a sub-contract UK manufacturer specialising in precision turned and milled components, the company has consistently sought innovative solutions to enhance operational efficiency. Founded 21 years ago, the Cannock-based company is intent on driving efficiency throughout the business. Leading the charge, managing director Greg Jackson recognised cutting fluid performance was an issue that needed addressing – the solution was found with
Oemeta and its Estramet S95 coolant.
As the first employee of the business some 19 years ago, Mr Jackson says: “We have an impressive variety of machining technologies with capabilities that include sliding and fixed head turning machines and vertical machining centres.” The plant list at Key Precision boasts well-known brands such as Citizen, Star, Hanwha, Haas Automation, DMG Mori, and Doosan. Oemeta’s Estramet S95 has delivered significant benefits for the manufacturer here.
Ryan Aviles, a technical sales representative at Oemeta, said: “Our relationship with Key Precision has been in place for a number of years. Ultimately, they didn’t have any particular problems with their previous coolant supplier, so it was about us biding our time and waiting for our moment – and then picking the right product for their needs. We came in and identified areas we could target for improvement, and that was when they invited us to trial.”
The collaboration between ISO:9001- and ISO:14001-certified Key Precision and Oemeta represents a sophisticated and methodical approach. Unlike traditional vendor relationships, Oemeta’s engagement began with an intricate, consultative process that prioritised understanding the manufacturer’s specific challenges and optimisation opportunities. Technical representatives evaluated the shopfloor environment and collected sample materials for rigorous laboratory analysis.
Performance-enhancing solutionBy taking fluid samples from machine sumps and sending them to Oemeta Germany for complete analysis that incorporates more than 50 different tests, the process is non-disruptive to ongoing production for end users. The six-step process includes sample capture, performance analysis, review of results, trial, product transfer and subsequently, a partnership. From the detailed analysis, Oemeta yields a 95% success rate in delivering a performance-enhancing solution. With such a hassle-free solution, more manufacturers should take up this golden opportunity from Oemeta. At Key Precision, the trial results were transformative, demonstrating Oemeta’s ability to deliver exceptional performance improvements.
Following the consultation process that included reviewing the machine processes and materials being machined, Oemeta identified Estramet S95 as the most viable solution. Compatible with steel, stainless and high-alloy steels, aluminium and aerospace grade alloys, Estramet S95 is perfect for the entire spectrum of applications from drilling, milling and turning to threading, honing, grinding and deep hole drilling. It is this flexibility that makes Estramet S95 the first choice solution among many sub-contract machine shops.
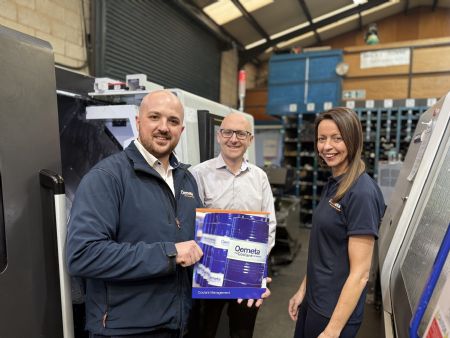
Mr Aviles continued: “Our first consultations tend to be an informal opportunity to meet the shop floor staff and decision makers to discuss issues and areas they would like to improve. We then take samples, send them to Germany for complete analysis, and utilise this information and discuss it in further detail with the customer. The improvements typically come from the first meeting and set of results. Once we have sample results, we can sit with customers and look at the opportunities in more detail. From the comprehensive performance analysis testing we undertake, we can benchmark against the existing product and even forecast the level of the benefits a customer will yield with absolute confidence – before our product even reaches their shopfloor.”
With testing that includes everything from lubricity and corrosion to long-term stability, foaming, water quality, employee and process safety, environmental impact and much more, Key Precision experienced remarkable efficiency gains, ranging from 35% to an extraordinary 150% across various machining operations. These substantial gains were achieved through Oemeta’s highly targeted approach, which was meticulously developed and implemented to match Key Precision's requirements.
Mr Jackson added: “In terms of percentage improvements with Oemata that we have monitored on set jobs, we have seen tool life improvements from 70% up to 150%. On every operation, we have seen a minimum improvement of 35%, and for long-running jobs, and with U-drills in particular, we saw a 77% increase. On parting-off, there has been an efficiency increase of 35% and turning operations have witnessed a 300% increase.”
The extended longevity and performance of cutting tools have been so dramatic that the company has recouped the annual cost of its Oemeta cutting fluids in the first month. As well as the cost savings and tool life improvements, machine and component cleanliness and quality has also improved.
Bio-sustainable operator-friendly fluidBased on synthetic ester oils, the translucent Estramet S95 is an alternative to traditional coolants and is free from mineral oil, boron, formaldehyde, fungicide, and active sulphur. This makes it a bio-sustainable operator-friendly fluid with incredible washing characteristics for both machine tools and components. As a highly stable fluid with a long service life and outstanding corrosion protection, Estramet S95 has increased tool life from 20% to 50% on most machines, which has generated significant consumable cost savings. Furthermore, the sub-contract manufacturer that works in the automotive, defence, medical, and telecommunications infrastructure sectors has witnessed a reduction in tool change frequency that has contributed to increased machine utilisation rates.
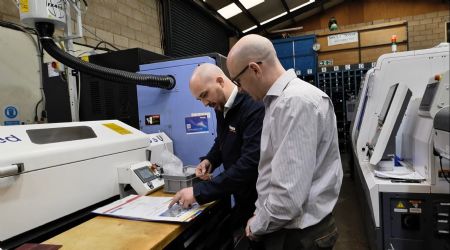
The implementation strategy transcended simple product replacement, incorporating a comprehensive approach that included bi-weekly site visits for sample collection, extensive laboratory testing, and careful compatibility assessments with existing cooling systems. A critical differentiator in OEMETA's service model is their commitment to continuous monitoring and optimisation. Their technical team conducts monthly coolant maintenance checks that go far beyond standard industry practices. These detailed assessments include concentration verification, pH level monitoring, microbiology testing, and proactive tank condition evaluations. This rigorous approach ensures sustained high performance levels and instils confidence in the product's long-term benefits.
Mr Aviles explained: “To track trials, we regularly re-visit the site; we are at Key Precision every two weeks to collect samples for our labs. With the results, we can give feedback to the customer and update them on how the product is performing. Once the trial is completed and the KPIs have all been achieved, we start the roll-out process. During this process, we take samples from all the other machines to check the condition of the machine tanks. We do this to ensure our coolant is compatible with the existing competitor's coolant. This minimises disposal and wastage costs as you can ‘top it over’ the existing products.”
The trial’s success has prompted Key Precision to commit to a comprehensive rollout across its water-based machining platforms. The partnership has continued to evolve, with plans for upcoming trials of Oemeta's oil-based solutions on the company's sliding head machines.
Mr Aviles continued: “This successful implementation isn’t the end of the journey. We are now looking at the neat oils. We have run the same tests on the neat oil in the sliding head machines, and we will deliver similar savings here, too, with our gas To liquid (GTL) product, which is an extremely pure and highly engineered product. All of our customers receive a regular standard service where they will see our team once a month. This visit will be to test coolant levels, the concentration, ph levels, and we’ll do the micro-biological dip slides too. This ensures the coolant is always retained within its optimal operating parameters.”
Mr Jackson concluded: “The trial results speak for themselves. We have committed to rolling the OEMETA cutting fluids and oils out across our full range of machines. The results so far have been fantastic, and we look forward to reaping more efficiencies and cost savings from working with Oemeta.”