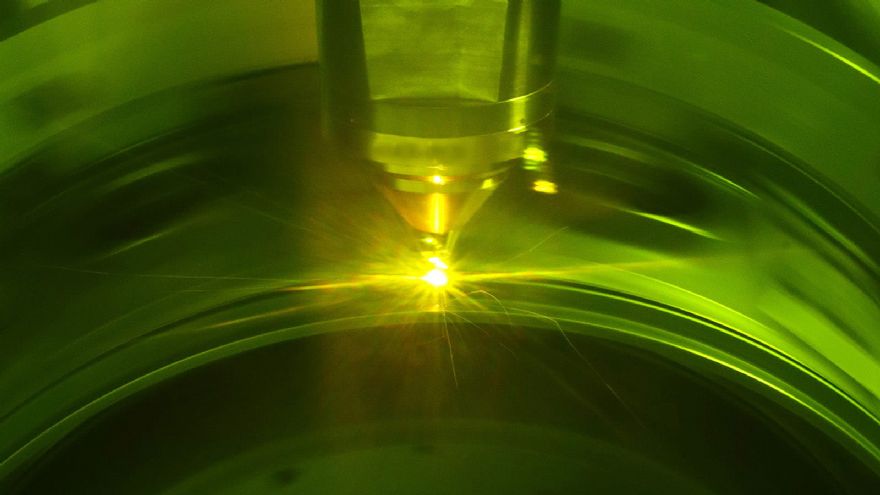
A new additive manufacturing (AM) solution has been developed by
Pratt & Whitney for repairing critical components for the company’s GTF engines, with the aim of reducing process times by more than 60%. The company is currently working to industrialise the repair, which will then be scaled and applied throughout the global GTF MRO network, with the expectation of recovering $100 million worth of parts over the next five years through implementing additive repairs throughout its MRO process.
Kevin Kirkpatrick, Pratt & Whitney’s vice president of aftermarket operations, said: “A more agile, additive repair process allows us to better serve our customers by improving turnround time while reducing tooling costs, complexity and set up. At the same time, additive not only reduces our dependency on current material supply constraints but also has the potential to support a range of critical GTF part repairs — and we are exploring additional opportunities for implementation.”
Developed by Pratt & Whitney’s North American Technology Accelerator in Jupiter, Florida, the new solution will enable repair to GTF structural case features using a 3-D printing method known as DED (directed energy deposition). By eliminating several steps in the current repair method, this new technology reduces overall process time by more than 60%, with the greatest benefits from minimising times for machine changeover and heat treatment cycles.
In April 2024, Pratt & Whitney announced expanding its use of technology accelerators to include advanced repairs, digital inspection, adaptive processing, and coating and masking for compressor and fan parts, blades, cases — and more.