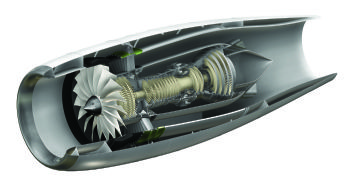
#ukmfg #engineering #aerospace @generalelectric @Bombardier #bombardier General Electric says that its Passport 20 engine — destined for the Bombardier 7000 and 8000 ultra-long range business jets — will be partly made from a new form of ceramic matrix composite (CMC) material, which could have a wide range of applications in the aviation industry.
GE is investing heavily to develop new materials that are lighter and can survive in higher temperatures. Such materials will allow designers to eliminate the elaborate cooling systems that are currently necessary to prevent metals inside the engine from melting.
The oxide-oxide CMC material replaces what would have been graphite-epoxy components in the Passport 20: a four-piece panel enclosing the engine core and a nine-piece component called a mixer, which is positioned in the exhaust flow of the engine.
Providing a weight saving of 18.1-20.4kg in the mixer components alone, the material is just one of several new technologies on the Passport 20 — including a 132cm-diameter fan blisk and ‘super-finish’ airfoils — that allow GE to claim an 8% fuel consumption advantage over the Rolls-Royce BR725.
GE has been developing oxide-oxide CMC materials for more than 20 years and selected oxide-oxide CMC for the Passport 20 engine in late 2010. Meanwhile, a silicon-carbide-based CMC material, which can survive even hotter temperatures than oxide-oxide, is being developed for CFM International Leap power plants. This replaces special metal alloys in the first-stage high-pressure turbine shrouds — one of the hottest parts of any turbo-fan.
The Leap-1A engine is due to enter service on the Airbus A320neo in 2015. Meanwhile, GE is already transferring the SiC-based CMC technology to the GE9X engine for the Boeing 777X, and expanding its use to the first-stage turbine blades and the combustor lining. Likewise, it is also looking to expand the use of oxide-oxide CMCs to other commercial turbofan engines — possibly including the GE9X.