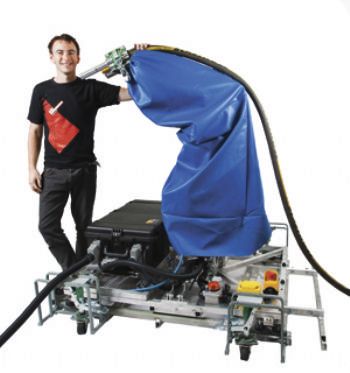
Using the Sydney Harbour Bridge as an example, Australian specialists have highlighted how service robots will soon revolutionise the way steel structures are serviced.
The robust robotic systems, which are planned to go into serial production at the end of the year, have at their core a lightweight arm designed by Schunk (
www.schunk.com).
The idea of automating the cleaning of steel structures was born in Sydney about seven years ago. Under the direction of Professor Dikai Liu — in co-operation with NSW Roads and Maritime Services, and the Centre for Autonomous Systems (Department of Engineering and Information Technology) at the University of Technology Sydney — an automated sand-blasting robot for servicing steel bridges was developed.
Today, Sabre Autonomous Solutions is responsible for the pre-commercial implementation of these robotic systems.
After a successful testing stage, the sand-blasting robot has become part of the standard equipment used by the maintenance team of the world-famous Sydney Harbour Bridge, which has a span of 503m and an arch crown height of 134m.
With some 52,800 tonnes of steel used in its construction, this is one of the heaviest and longest steel-arch bridges in the world.
As with any steel bridge, the Sydney Harbour Bridge must be continuously maintained and protected against corrosion. This includes sand-blasting and repainting 485,000m2 of steel — the equivalent of about 68 football fields.
Moreover, a single coat of paint requires about 30,000 litres. Rosie and Sandy — the two blasting robots — work tirelessly blasting dirt, rust and old paint from the steel girders; and while some workers have to take a break every 15-30min due to the extreme physical strain, the two robots blast their way through metre after metre without interruption.
Taking about 50min to complete a segment, they use sensors, special algorithms and a mapping system to calculate the optimum path, avoiding collisions. Operators monitor the sand-blasting process from a safe distance.