Heavy-duty precision machining
Posted on 12 May 2010. Edited by: Machinery Market. Read 1678 times.
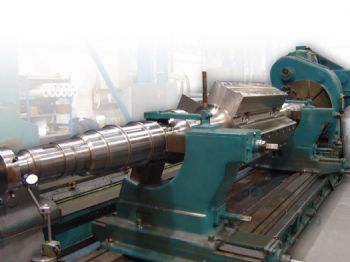
The bearing surfaces on a 7.4-tonne rotor have been precision-machined by Manchester-based BEP Surface Technologies in preparation for final turning operations by Boro Foundry, which manufactured the shaft for Converteam — the energy conversion technology specialist. Designed for use in a gas turbine power plant in the USA, the rotor is 5.6m long and has an outside diameter of 475mm. To facilitate the installation of vibration-monitoring equipment, BEP ground all the bearing diameters and thrust faces to 0.005mm TIR and the outside diameter to a surface finish <16 CLA.
Boro Foundry, which supplies a wide range of castings and machined parts, produced the rotor from a pre-machined forging supplied by Converteam. The turning operations were carried out on an 8m-long Tuscan LL950 CNC lathe — the only one of its kind in the UK. Following the grinding work by BEP, vibrator probe tracks 0.0025mm deep x 30mm wide, with a surface finish >0.063 RA, were diamond-burnished into the shaft at Boro Foundry’s site in Stourbridge. Accuracy to these tolerances is essential to balance the shaft and to ensure that it fits into a bearing that houses two vibration transducers.
BEP has expertise in turning and grinding all kinds of large-diameter heavy rolls, cylinders and shafts to very fine tolerances. Its grinding machinery can handle steel mill rolls and large chill rolls weighing up to 10 tonnes, while diamond turning and polishing can be carried out on diameters up to 1,100mm. In addition to the usual finishes on steel, cast iron and chilled iron, the company can grind copper, chrome, nickel and even rubber. Diamond grinding of plasma-sprayed coatings such as tungsten carbide and ceramics can also be undertaken.