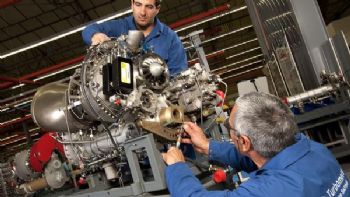
Helicopter engine manufacturer Turbomeca has started serial production of parts using the latest additive-manufacturing process at its Bordes facility in France, which is one of the first of its kind to produce additive components in volume for France’s aerospace propulsion industry.
Arrano test and production engines will feature fuel-injector nozzles made using Selective Laser Melting (SLM) techniques. This process will also be used to manufacture Ardiden 3 combustor swirlers.
These engines are Turbomeca’s latest models, and they are among the most advanced turbo-shaft units ever designed.
Unlike the traditional manufacturing processes of forging and machining, which are based on material removal, additive manufacturing builds layers (each between 20 and 100µm thick) of fine metal powder to produce complex-shape parts.
In the case of SLM, a computer-controlled laser shoots pinpoint beams onto a bed of nickel-based super-alloy powder to melt the metal in the desired areas.
Additive manufacturing also simplifies the manufacturing process. A traditional fuel-injector nozzle is made using dozens of different pieces.
The Arrano component comprises a single piece of material — plus it features advanced injection and cooling capabilities. One SLM machine is already in service and qualified for mass production; others will come on stream over the coming years.