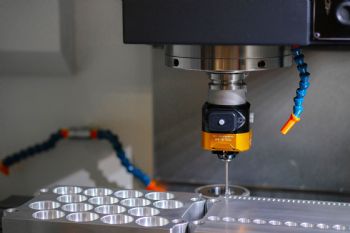
ActiveEdge Apex, the latest fully automated fine-boring head from Cornwall-based Rigibore, delivers new levels of control in setting and maintaining critical tolerances through a fully automated process.
Making use of Rigibore’s ActiveEdge technology, Apex is said to be ‘a world first’ in terms of fully integrated automatically adjustable fine boring heads, delivering precision performance on bores ranging from 0.25 to 26mm in diameter.
Rigibore will unveil the Apex system at
EMO 2019 (Hall 4 Stand D03), which has a theme of ‘smart technology driving tomorrow’s production’, therefore providing the perfect opportunity to showcase this solution.
With the manufacturing industry’s ever higher expectations regarding the production of high-value components, Apex’s auto-compensating system creates significant and lasting benefits in terms of reduced machine down-time, improved part quality and operator safety.
Of greater significance, however, is the ability to consistently meet and maintain critical tolerances, while at the same time eliminating the risk of scrapped parts.
The Apex boring head uses a closed-loop compensation system that automatically adjusts the diameter being cut as a result of commands sent from the machine tool’s control, based on values calculated by in-process measurements.
The boring head is adjusted with micron accuracy, completely independent of operator intervention.
Compensations can be made with the head in the spindle or even while it remains idle in the tool carousel while another operation takes place.
Assurance that the correct adjustment value has been made is confirmed by direct feedback from the tool to the ActiveEdge interface.
EMO provides the ideal platform to build on what has already been significant interest in the automated Zenith solution from Rigibore customers in the aerospace, automotive, wind power and injection moulding sectors, where consistent bores and uninterrupted production are of primary importance.
Rigibore chairman Roger Bassett said: “Typically, manufacturers experience all too familiar problems with conventional boring heads — mainly the headache of accurately setting and maintaining fine tolerance limits, with high scrap rates impacting on bottom-line performance.
“The requirement for operators to constantly check boring heads for accuracy, which slows production, can now be eliminated.
“Rigibore’s Apex boring head provides a perfect bore first time and every time, using macros to accurately adjust the boring head within predetermined tolerance parameters, all while reducing cycle time.”