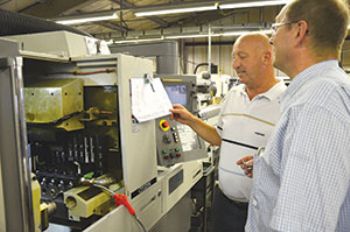
Sandy-based Ionic Engineering (
www.ionic-engineering.co.uk), a dedicated user of CNC sliding-head turn-mill centres, currently exports half of its sub-contract machined components — largely for the switchgear, safety valve and electrical sectors — to Europe and the USA.
Indeed, the company’s success has been such that sales have doubled since 2008, and it is currently spending some £400,000 on a machine shop extension and new equipment.
Managing director Ian Fitzwater attributes much of the success of his 22-people business to the turn-milling of components up to 42mm in diameter and to his team of three — plus a recent trainee-operator — who run the turning section under works manager Neil Titmus.
Since 2008, Mr Fitzwater has bought five Citizen sliding-heads machines and one Miyano fixed-head turning centre — all from Bushey-based Citizen Machinery UK Ltd (
www.citizenmachinery.co.uk); the phased introduction of these machines has meant that Ionic has benefitted from the on-going improvements in their design.
Meanwhile, the expansion of its 8,000ft2 production shop — with a 2,700fsq ft extension that will become the turning centre housing the Citizen and Miyano machines — will provide extra floor area in the main factory for new machining centres and support services (the company also has a further 2,000sq ft facility just down the road, plus a sheet-metal operation).
Ionic Engineering was formed in 1988 when Mr Fitzwater’s employer decided to close the machine shop at the company where he was production manager. Mr Fitzwater was able to acquire the machines and took on nine people to provide a sub-contract machining service covering industrial switchgear, switch bodies, linkages, indicators and safety-related items such as explosion-proof housings.
In 2008, Mr Fitzwater installed his first Citizen — an L20-Vlll — which “completely opened our eyes, immediately bringing new opportunities. From that day on, we forgot about secondary operations, fixtures and even gauges on turning work, as we focused on what could be achieved with single-cycle sliding-head processing.”
The company operates with single flexible shifts between 4am and 6pm; and on suitable components, machines are left to run unmanned through the night. Most batches tend to be between 50 and 200 on materials as diverse as 303 and 316 stainless steels, aluminium, a range of steels, brass, copper and plastics.
Cycle times on the Citizen machines vary between 11sec and 15min (considerable amounts of in-cycle milling and engraving are involved in these longer cycles).
The smallest part is a stainless-steel component 2mm in diameter x 2mm long. Produced on either a Citizen B16 or L20X from 6mm-diameter bar, it has a radius dome end and a groove in the outside diameter 0.5mm wide and 0.5mm deep; it is produced in batches of 1,000 in a cycle time of less than 18sec.
The largest shaft produced is 32mm in diameter x 250mm long; it has double threads at each end. The Miyano BNA-42S, which was installed in 2011, is mainly engaged on larger-diameter bar work — up to 42mm — that can involve very complex cycles.
Mr Titmus says that 80% of new programs are created at the machine using ‘cut and paste’ from other proven cycles; the remaining programs are prepared off-line using Citizen’s Alkart CNC Wizard programming aid. As for the accuracy of the Citizen machines, he refers to a small silver-steel component that required turning operations and the milling of an eccentric feature.
Ionic had allowed for specialised grinding because the overall tolerances were 5µm, while the tolerance on the milled eccentric was just 4µm. “We had concerns over how we would hold the part for grinding, so we took a flyer and machined 50 parts to final size, then measured each 100%.
To our surprise, there were only very minimal changes in size, so we ran the order in batches of 100 and repeated our checks on each part; all passed.”