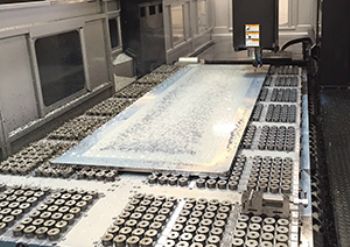
When Hereford-based TRP Sealing Systems (
www.trpsealing.com) invested in the UK’s first Wele large-bridge machining centre (from 2D CNC Machinery) as the mainstay of a new venture — manufacturing and refurbishing mould tools in-house — it turned to Eclipse Magnetics (
www.eclipsemagnetics.com) for an effective method of securing large steel plates and existing moulds in a known and repeatable position.
The moulds are from 16 to 30mm thick, while the plate dimensions range from 860 x 830mm up to 3,900 x 1,750mm. The key to the project is to ensure that the plates are held flat during machining, so that the back face to mould profile is totally parallel — and also to provide clearance for back chamfering (without this, the moulded product would be scrap).
Eclipse suggested a Power Matrix permanent electromagnetic chuck, with a magnetic bed that was supplied in 14 sections.
The overall size of the Power Matrix milling system is 4,000 x 2,000 x 66mm. Using high-intensity neody-mium magnets to provide consistent and uniform clamping over the entire workpiece, it allows five-side access to the workpiece. It also reduces vibration and chatter, extends tool life and improves the surface finish of the product.
John Urbanski, engineering manager at TRP, said: “The Power Matrix has enabled us to not only reduce our set-up time significantly but also ensure that the tool manufacture is of the highest quality possible.”