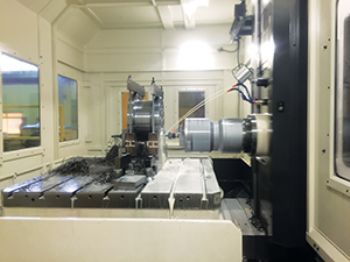
By listening to the production requirements of Howco Bredbury (
www.howcogroup.com) and modifying an already high-specification machine to meet them, Sheffield-based TW Ward CNC Machinery (
www.wardcnc.com) was able to win a substantial two-machine order from the Stockport-based precision machinist.
The latter supplies equipment that is used in down-hole, sub-sea and surface systems, and when managing director Ian Booth needed to improve drilling cycle times on a sub-sea component, Ward CNC came up with a solution that allowed internal features and contours to be machined in the same set-up as drilling.
Mr Booth says: “The production of a single 170mm-diameter hole through steel billets of various sizes up to 1m x 800mm square requires a machine with the appropriate torque, and Ward CNC seemed to be the only machine supplier that was able to provide a suitable solution.”
A Hartford PBM 115A CNC horizontal boring and milling machine was the answer. “The first requirement was for a relatively small spindle, which the PBM has, to allow easy access; and while the spindle speed of 2,500-3,000rev/min was fine, more torque was needed to enable the machine to consistently ‘push’ the 170mm holes through the billets. Ward CNC’s answer was to uprate the Z-axis motor from 30 to 55Nm.”
In addition, Ward CNC increased the W-axis drive ratio by changing the ballscrew pitch from 12 to 8mm to prevent the additional Z-axis torque ‘pushing back’ the W axis.
Finally, Ward CNC engineers interfaced a Cogsdill facing head and four line bars for the final contouring and feature machining of the workpieces. All these modifications were undertaken by Ward CNC at its Sheffield headquarters. They were fully endorsed by Hartford, which then supplied an identical machine direct from Taiwan.