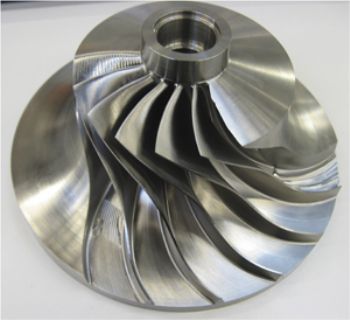
In this article, the EDM and milling machine tool specialist GF Agie Charmilles provides an insight into the ‘problems’ associated with machining titanium and how these can be avoided or overcome.
The company (www.gfac.com) says titanium has many properties that make it the material of choice for designers and manufacturers, as parts made from it weigh roughly half as much as steel equivalents. Titanium is also renowned for its high strength and good elasticity, as well as its anti-corrosion and anti-oxidation characteristics — which is why it is increasingly being specified for use in motor-sport, automotive, aerospace, power generation, oil and gas and medical applications. However, many of the qualities that make titanium so appealing also make it difficult to machine.
Titanium is a poor conductor of heat, which means that the heat generated by the cutting action does not dissipate quickly; most of it is concentrated on the cutting edge and the tool face, which can result in cutting-tool deformation, reduced tool life and potential workpiece damage. Furthermore, titanium can alloy and react with the materials used in cutting tools, resulting in galling, welding and smearing, as well as rapid deterioration of the cutting tool.
Because titanium is more ‘elastic’ than steel, workpieces have a tendency to move away from the cutting tool unless ‘heavy’ cuts are maintained. However, intricate (thin-wall) parts can deflect, causing chatter, tool rubbing and tolerance problems. Furthermore, the material’s surface integrity can be compromised when certain machining techniques are used — especially grinding and EDM.
Titanium’s work-hardening characteristics are such that titanium alloys demonstrate a complete absence of built-up edge. Because of the lack of a stationary mass of metal (built-up edge) ahead of the cutting tool, a high shearing angle is formed. This causes a thin chip to contact a relatively small area on the face of the cutting tool, resulting in high loads per unit area. These high loads, combined with the friction developed by the chip as it rushes over the contact area, results in a great increase in heat on a very localised portion of the cutting tool. Furthermore, the combination of high loads and heat produces cratering action close to the cutting edge, resulting in rapid tool breakdown.
Milling titanium
Two major challenges in the machining of titanium are achieving fast metal removal rates and improving tool life. Recent advances in machine tool and tooling technologies allow both objectives to be met. Many factors are important in determining the optimum methods of manufacturing titanium components and what removal rates can be expected — and achieved.
Principally, there are two machining methods that can be used when machining titanium: heavy-duty cutting (sometimes referred to as high-performance machining or HPM); and high-speed cutting (sometimes abbreviated to HSC or HSM).
Heavy-duty cutting involves high-volume removal rates and necessitates the use of high power, high torque and low cutter speeds. This method is often used for roughing operations. High-speed machining is generally used for moderate roughing and finishing operations; it allows manufacturers to achieve final part accuracy and good surface finishes. Typically, the goal in high-speed machining is not high metal removal rates, but good part accuracy and a fast finishing speed.
In addition to the machining technique used, tooling, spindle speed, depth of cut, feed rates and the machine tool itself come into play. With regard to tooling, it has already been mentioned that titanium is a poor thermal conductor with ‘elastic’ properties; and while using the right tool can help to mitigate these challenges, use of the wrong tool will only compound them. Because titanium tends to work-harden during normal cutting operations, tools that are unable to cut through the depth of hardened material will actually accelerate the hardening process. So, instead of cutting, a wrong tool will push against it, straining the material; and as the material reaches a higher level of hardness, cutting speeds that were appropriate at the start of the cut will become excessive, wearing down the cutting tool quicker than normal. Many variables must be considered when selecting the most effective tooling solution, and these variables — including tool diameter, tool coatings, tool type, number of teeth and spindle speed — will all have an impact on performance and the cost per part. An appreciation of cutting-tool coatings and their effects is particularly important.
Importance of coolant
Coolant also plays a crucial role, and if this is not applied appropriately — or if the ‘wrong’ coolant type is used — tools will wear quickly or fail. When machining at high speeds, ineffective chip evacuation is always a potential point of failure. If chips fall back into the chip/tool/ workpiece interface or do not clear the cutting area, the re-cutting of chips will inevitably cause damage to the tool and/or workpiece. In addition to chip evacuation, super-heated chips tend not to break into smaller pieces, compounding the problem of chip removal.
Another coolant issue when machining titanium is the problem of poor lubrication. This is often caused by the coolant pressure not being sufficient to push through the tool tip during high-speed machining operations; coolant can also be vaporised by the high temperatures generated during the cutting process. When machining titanium, the tool tip can reach temperatures as high as 2,000°F, which is sufficient to cause super-heated steam to form in water-based coolants, causing the coolant to vaporise before it even touches the workpiece.
The specification of the machine tool itself should not be overlooked; a rigid, thermally stable machine with a ‘stiff’ tooling interface is important if the effects of vibration and heat generation are to be minimised. High-torque spindles with a through-spindle coolant capability are essential; machines should also be capable of achieving higher spindle speeds for drilling and finishing operations. Tool measurement and inspection systems that can identify worn or broken tools are also considered essential.
To optimise the performance of the machine tool during different machining operations (such as roughing and finishing), and to take account of different and changing machining priorities (removal rates, part accuracy and surface finish), it is important to be able to alter a machine’s settings to achieve the desired outcomes. Systems such as OSS (operator support system), which is accessed via the machine’s control on GF Agie Charmilles HPM and HSM milling machines, allow such re-calibration to be achieved.
Also important is a warning system that alerts operators when excessive vibrations are being encountered during machining (caused by interrupted cuts or poorly balanced tools, for example). Systems such as APS (advanced process system), which is available on GF Agie Charmilles machining centres, help to maintain accuracies, improve tool life and achieve greater process reliability.
EDM and titanium — no longer incompatible
GF Agie Charmilles’ advanced digital-generator technology (available on its latest wire-cut EDM machines) limits the negative effects of electrolysis and surface pollution when machining titanium. Before the availability of CleanCut digital technology, the wire-cut EDM machining of titanium parts created a number of headaches for users, the most common — and the most noticeable — being the unwanted effects of electrolysis.
When titanium is machined, an oxide is formed due to passivation, and this oxide layer is usually coloured grey. However, when titanium is EDM-machined, extra passivation occurs, turning the oxide layer blue. While the structure of the titanium is unaffected (the ‘blue tinge’ corresponds to an oxide layer 70nm in depth), the result is unsightly and requires secondary finishing operations to remove it.

CleanCut technology eliminates the bluish tinge via Nil Mean Voltage settings. What this means is that, unlike conventional EDM technology, which produces ions that are suspended in the water and bombard the surface of the titanium workpiece, the positive and negative charges generated alternately with CleanCut technology balance out the mean voltage.
This technology also avoids the surface pollution that results from the ‘re-depositing’ of wire particles after machining (when some of the tiny droplets of copper and zinc ejected from the wire by every discharge remain on the part). This pollution is particularly problematic when machining titanium for medical applications, as the bio-compatibility of titanium can be compromised by these copper particles. The unique shape and characteristics of the spark created when using the CleanCut generator mean that the ‘cleanliness’ of a part can be greatly increased, reducing the need for additional operations.
Agie Charmilles strategies for successful machining
- Use positive cutting geometries to minimise cutting forces, heat generation and part deflection
- Use constant feed to prevent work-hardening of the workpiece during machining
- Use an optimum coolant strategy to preserve thermal stability and to prevent temperature build-up that can lead to sub-surface irregularities and possible tool failure
- Keep tools sharp; dull tools exacerbate heat build-up and cause galling and seizing that can lead to tool failure
- Machine titanium alloys in the softest state possible (many alloys get harder when heat is applied or generated)
- Use a large tool-nose radius or round inserts whenever possible to put more of the tool into the cut; this decreases the cutting force at any one point and prevents localised damage
- Make sure the machine tool is up to the job (rigid and thermally stable construction; advanced spindle technology; powerful and responsive control system; effective chip removal; flexible coolant delivery systems; in-process tool measurement and inspection).
Machining a titanium impeller
Material: titanium (Ti6Al4V) billet
Machine: Mikron HPM 800U machining centre
Part characteristics: 100mm high; 18 blades; entrance side (outer diameter 112mm, blade height 36mm); exit side (outer diameter 200mm, blade height 8mm)
Machine characteristics: simultaneous five-axis machine; 20,000rev/min in-line spindle with through-spindle coolant capability; HSK A63 tool interface; direct-drive A and C axes
Machining strategy: one blade machined at a time and then repeated
Roughing operation 1: 2,000rev/min using an 8mm-diameter end-mill; 220mm/min feed; step-over 6-8mm; cutting depth 8mm; removal rate 14.08cm3/min
Roughing operation 2: 5,500rev/min using conical ball-nose end-mill (3mm diameter); 495mm/min feed; step-over 0.13mm; cutting depth 10mm
Finishing operation: 10,000rev/min using conical ball-nose end-mill (3mm diameter); 1,000mm/min feed; step-over 0.17mm
Total machining time: 60min per blade.