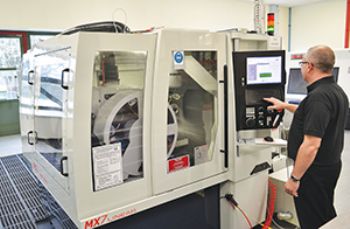
Global precision engineering company Renishaw plc (
www.renishaw.com) is a world-leading engineering technologies business, supplying products used in applications ranging from jet engine and wind turbine manufacture to dentistry and brain surgery.
In September 2011, the company purchased a 193-acre site with 460,000sq ft of buildings in Miskin, near Cardiff, for £7.7 million. There followed a further investment of £32 million in refurbishment and the purchase of CNC machine tools and electronics assembly systems.
Given the high volumes of precision components with demanding dimensional tolerances produced by the Miskin facility, tooling performance is of vital importance. Moreover, the ability to quickly source custom-made tools is an occasional requirement.
To ensure the continued availability of the most appropriate standard tooling, Renishaw recently installed an Anca MX7 Linear tool and cutter grinder at Miskin, so that the site can manufacture and regrind most of its own tools in-house.
Development engineer Aled Beswick said: “An Anca tool and cutter grinder installed at Renishaw’s Stonehouse plant has given excellent service for over five years. We were aware of the technical progress made in this type of machine and evaluated several alternatives.
The Anca MX7 Linear proved ideal for our needs, and we specified one with an Anca robot loader and a Renishaw HPRA probe system; this allows us to reduce set-up times and increase unmanned running times.
“Our large number of high-precision machine tools need a constant supply of premium-quality round carbide tooling, so the ability to manufacture and re-grind our tools in-house gives us a number of benefits.
"For example, we can evolve and develop the designs of commonly used carbide tools to achieve increased productivity and enhanced component quality; and given the long lead times for bespoke tools and the high costs quoted by tooling manufacturers, it is an advantage that — with the help of Anca’s easy-to-use Toolroom software — we can quickly design and produce custom-made tools for some of our more unusual applications. We are also a large consumer of round carbide tooling, so our policy of producing and re-grinding our own tooling in-house has significantly reduced our tooling costs.”
The MX Linear range of tool grinders has been designed to meet the needs of tool production facilities requiring maximum output with optimised flexibility. They use the latest cylindrical linear-motor technology for high levels
of accuracy and performance; they also feature a robust design that is based on a bi-symmetrical gantry, while Anca’s Toolroom software ensures that MX Linear machines can efficiently handle all manufacturing or re-grinding challenges.
MX Linear machines use Anca’s LinX linear motors — in conjunction with linear scales — for the X and Y axes. These provide high axis speeds and high rates of acceleration while maintaining a smooth axis motion, resulting
in reduced cycle times.
Moreover, they are not susceptible to wear and are not affected by temperature variations, as they have no contacting parts — plus they are sealed to IP67 against the ingress of grinding contamination. These factors ensure a ‘lifetime of efficient operation in harsh grinding environments’; and because the created magnetic field is cylindrical, no additional down force is placed on the rails or machine base.
LinX motors use less energy than an equivalent flat-bed-type linear motor, and they have the same power consumption as a ballscrew system, although they are more efficient. Another advantage of their design is that they naturally isolate any heating effects from the machine. Indeed, their low heat load means that LinX motors do not need a separate chiller unit; they use the machine’s regular coolant system, reducing both floor-space and power requirements.
The MX7 bought by Renishaw is the most powerful tool and cutter grinder in Anca’s Linear range. Its 38kW permanent magnet spindle provides high torque at low spindle speeds, which is ideal for carbide grinding as well as a wide range of other applications.
The Robo-Mate robot loader uses a Fanuc robot that takes tools directly from the pallet to the collet in a single grip. The automated system is available with two pallets as standard, although a four-pallet option is available. RoboMate can load tools from 3 to 32mm in diameter and up to 350mm long.