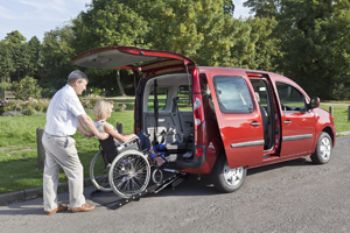
Making vehicles ‘wheelchair-accessible’ is big business for Sussex-based Constables Ltd, which is currently converting over 1,000 vehicles a year. This has earned the company the No 2 spot in the UK for this type of work, and it plans to branch out into Europe in the near future.
Constables currently undertakes conversions of Citroen, Renault, Peugeot and Nissan models, working closely with the vehicle manufacturers on the design of the conversions, plus the materials and parts used. Conversions have to be certified by the VCA (the UK’s national approval authority for new road vehicles); this is hardly surprising when one considers that providing wheelchair access involves removing a substantial part of the vehicle’s ‘back end’, followed by the installation of a new floor pan, rear and front beams, a new fuel tank, a new exhaust, gas struts and after-market seats, plus assorted brackets, fasteners and catches — not to mention a considerable amount of re-upholstery and re-trimming to return the vehicle to ‘showroom condition.’

Indeed, managing director David Constable says the conversion process is undertaken to a standard similar to that of the original vehicle build. The kit used to convert a vehicle includes every part and sub-assembly — right down to glues and sealant. There are also jigs for every cut that is be made, and every step required for the entire conversion is meticulously detailed and documented. This level of procedure is essential to conforming with the high legal standards that apply — and to be able to complete some five conversions a day, each within
an overall time of around 17hr.
Need for change
Less than three years ago, Mr Constable’s business was operating on a somewhat smaller scale. “It was more of a cottage industry then. We were working in 20,000ft
2 premises with a
1/2 acre of land at Pevensey, in Sussex, and we relied on four sub-contractors to manufacture most of the parts required; our focus was on the design and the actual conversions. However, our lease was about to expire and we needed to move.
“We found premises at Golden Cross, a few miles up the A22 from where we were. The move happened to coincide with an improvement in the market; it also saw us renew our emphasis on sales and marketing, our aim being to become a marketing-led company that makes its own product. The business was growing rapidly, much faster than our four suppliers could keep up with; and in what was becoming an increasingly competitive market, we needed to be making conversions more cost-effectively.”
It was in February last year, while pondering this predicament over a cup of tea that Mr Constable decided to bring all manufacturing in-house — a decision made somewhat easier by the availability of a second unit adjacent to the one they already occupied at Golden Cross. He was able to take this over a few months later (in June), and he recalls standing in some 30,000ft
2 of empty — and somewhat dilapidated — factory space (formerly a joinery company) with a degree of trepidation. This was hardly surprising, as he now had two factories totalling some 50,000ft2 and 4.5 acres of land. That said, his planning and costing had been meticulous, and he had total confidence in the project, as did his bank manager — so much so that Mr Constable was an area finalist in HSBC’s Business Thinking awards.
Detailed planning
The tremendous amount of investigative work and planning undertaken following the ‘project start’ in February was based on the production of 300 conversion kits a month — three-times the company’s own conversion capacity, but sufficient for its European expansion plans. Mr Constable and his engineering team detailed all the machinery and equipment they would need to achieve this — and how it would be phased in to raise productivity in a manageable way.

Based on the recommendation of a business associate — and on subsequent technical discussions — Coventry-based Bystronic UK Ltd (www.bystronic.com) was selected to supply the major items of sheet metal-working equipment. For profiling, Mr Constable bought a Bystronic Bysprint 3015 laser cutting system, together with a ByTrans Extended automatic load/unload system; the former has a 3.3kW laser and a cutting area of 3,000 x 1,500mm, while the latter provides either six tonnes in two cassettes of uncut material, or one cassette of raw material and one for offloading the picked parts from a nest. The cut waste skeletons are offloaded into
a third lower level. The materials processed are predominantly stainless steel, mild steel and aluminium.
For forming, Mr Constable bought a Bystronic Xpert 150 hydraulic press brake; this has a 150-tonne capacity, an overall bed length of 3,100mm and a six-axis back-gauge range of 600mm. It also features a hemming table for producing safe edges without tool changing and a row of LEDs above the upper beam that show the back-gauge position and flash when changing tools to show where they need to be located. Tool changing takes seconds as all the tools are stored in a motorised tool magazine and clamped/unclamped by the push of a button through the machines hydraulics. “The Bybend software creates bending sequences automatically, indicates what tools need to be used and where they need to go — de-skilling the task of the operator,” says Mr Constable.
Also bought were two robotic welding cells, a Timesavers deburring machine, a Faro Gage measuring arm and a powder coating plant. “As it happens, introducing the ABB robotic welding cells, which feature CMT — cold metal transfer — welding required the most engineering work and product redesign, but the benefits have been significant. Manually welding a stainless-steel fuel tank took 165min; a robot does the job in 14min.
“Automation is key to minimising costs, which is why we have left space by the laser for the later installation of a Bystronic ByTower raw material and cut-part racking system, which will load and unload the laser via the ByTrans automatically. Our aim is to run the laser during the day shift as well as ‘lights out’, with the rest of the factory operating on a single shift.
“It is almost frightening the speed at which the project has developed; from the idea of in-house manufacture to producing our first kit of parts took just 10 months, but we now have far greater control of our future.”
I