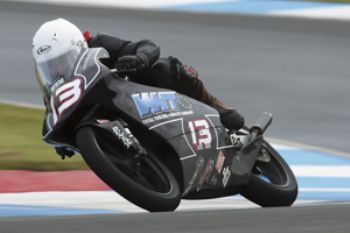
In its 8 December 2011 issue, Machinery Market published the feature The magic of manufacturing (
www.machinery-market.co.uk/burman . . . see page 16), which highlights Sam’s passion for making things, programming CNC machines and racing motorcycles. Here, she describes her training on XYZ machines at WNT’s Sheffield showroom and some of the parts made:
I race a Honda RS 125cc GP motorcycle in the Monster Energy Motostar British Championship under the WNT/Phil Burman Racing team name. I am also an apprentice-trained mechanical engineer working as a machinist at Tata Steel in Scunthorpe. My story was featured in a previous issue of Machinery Market, and now I would like to share my experiences after taking up the fantastic offer made by WNT’s Tony Pennington and XYZ’s Nigel Atherton of operator training and use of the machines and tooling at WNT.
In the week before Christmas, I spent two mornings training with Mike Corbett, XYZ’s applications manager. On leaving home the first morning, I was extremely apprehensive about using the new milling machines and lathes; prior to meeting Machinery Market editor Colin Granger at a race meeting, my engineering career had been quite sheltered. It was mainly based on working in the Tata Steel machine shop, where most of the machines are conventional — albeit large. I was also very excited; I would love to have my own business making parts for racing motorcycles, and this could be the start.
Mike Corbett has an interest in motorbikes and racing, so I felt at ease straight away; and although time was tight — I had to get back for a 2-10pm shift — I found the operating systems on both the ProtoTrak lathe and mill surprisingly easy to use. With Mike’s help, I was soon familiar with the controls, and within a matter of hours we were using my ideas to produce meaningful parts. During this initial training period, I was very kindly given software for ProtoTrak programming off-line on my laptop. All the controls and functions appear exactly as they do on each machine. This was a massive confidence booster and helped my subsequent training no end.
After the second training session, I left confident that I could operate the machines by myself; and thanks to Mike’s enthusiasm and support, I also left with a new design of foot-rest to try out. This was both stylish and functional, and it subsequently formed the basis of a demo part that XYZ produced on its stand at the Autosport show earlier this year. The part is machined from solid; it is first turned and knurled on a lathe, then finished on a VMC with a fourth axis. It has also been produced in both ‘wet’ and ‘dry’ versions with different depths of knurl; and thanks to the poor weather this season, both types have been tested. Moreover, they have subsequently been purchased by a British Championship-winning team.
Better and lighter

Over the Christmas holidays, I considered other simple parts that I could make to familiarise myself with the ProtoTrak machines — hence the sub-frame project. I am a petite rider, and some years ago me and my dad Phil — a self-taught craftsman and former championship winner — decided to shorten the seat, which we achieved by altering the sub-frame. Since that first effort, it has become a bit of a Burman tradition before the start of the season to make this part — and others — better and lighter. Come Christmas, Dad had already started on the cardboard cut-outs for this season’s sub-frame, which basically consists of two aluminium box-section ‘arms’, spacers, bolts and irregular-shaped plates. The latter are formed around the motorcycle frame, then welded to the sub-frame, allowing it to be bolted to the main frame.
I reckoned the plates would make an ideal starting point for my next visit to WNT to use the XYZ ProtoTrak machines. I first drew the design on graph paper, decided on my datum edges, then used the ‘irregular profile’ and ‘irregular pocket’ options within ProtoTrak to quickly input all the co-ordinates required to produce the plates. I also used the ‘look’ feature as I went along, to make sure that I was moving in the right direction — all done off-line on my laptop.
Prior to my first ‘solo’ visit to WNT, I had cut two lengths of stock for the plates, drilled the mounting holes and made a simple jig out of steel section, so that I could locate and clamp each plate for machining. With regard to tooling, one of WNT’s sales team recommended the optimum tooling, as well as the best cutting feeds and speeds to suit the material and set-up. All the WNT staff I’ve met have been friendly and helpful, and I have felt comfortable asking their advice. As the weeks have passed, I’ve got to know the ProtoTrak machines well, particularly the mill. The control is very user-friendly, and the machine is easy to set up and run small batches on. With the lathe, I have mainly used the DRO screen to produce one-off parts, making good use of some of the control’s features, including Do One Events for chamfer and radius. This allows you to make simple moves without needing to create an entire program.
More recently, I’ve been designing foot-rest hangers, for which lightness and aesthetics are now the main considerations.
Prior to the support offered by WNT and XYZ, I was having to straighten and repair parts like this after a crash. Now, I can make new parts — and more-complex ones at that. These will be followed by sets of fork yokes, for which the tooling, work-holding and machining processes will require a lot more thought. I am also pleased to say that, although I crashed out at the third round of the British Superbike series at Oulton Park, the new foot-rest did what it was meant to do — help minimise damage to the bike while ‘sacrificing’ itself in the process.