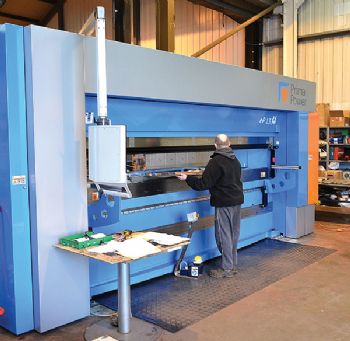
Kings Lynn-based Dale Sheetmetal Ltd provides a wide range of precision sheet-metal services — mainly to the ‘food service’ and catering sectors, but also to an increasing variety of industries.
Established for more than 40 years, the family-run concern’s customers are mainly based in East Anglia, although many companies nation-wide are now using Dale Sheetmetal’s supply and installation service.
The company, which undertakes the precision CNC punching, cutting, folding and bending of ferrous and non-ferrous sheet materials, can accommodate sheet up to 4 x 1.5m and 6mm thick.
To increase its bending capacity and capabilities, managing director Dave Dale recently bought a servo-electric press brake from Coventry-based Prima Power UK Ltd (
www.primapower.com).
Although smaller versions of eP-series machines have been installed in the UK, the large eP 1336 variant (with a press force of 135 tonnes and a bending length of 3,655mm, as purchased by Dale Sheetmetal) is the first of its kind installed in the UK.
Mr Dale said: “Over the past two decades, Dale Sheetmetal has earned a reputation for delivering high-quality work, on time and on budget. We are able to achieve this by employing highly skilled engineers and fabricators and by using the best-available production equipment and design technologies.
“We use the latest CAD software, which is fully integrated with our CNC punching, laser cutting and bending machines. Once the design has been loaded into our system, it is sent directly to the control console of the appropriate machine via our wireless network.
“Each stage of our company’s development, including our recent factory expansion, has been driven by growing customer demand. Having identified bespoke bending as a ‘pinch point’, we investigated the latest press brake technologies; and rather than consider a conventional hydraulic press, we only looked at next-generation all-electric machines.
“Now installed and fully operational, the eP 1336 ensures that we can produce large volumes of consistent high-quality work. Moreover, the extra capacity created by our new servo-electric press brake will allow us to tackle new markets.”
'Green' technology
Prima Power has been applying servo-electric technology to sheet metal-working for a number of years; its first product with ‘green’ e-technology — a punching machine — was introduced in 1998.
Today, this technology is offered across a wide range of company products; applied to press braking, it ensures machines that combine productivity, accuracy, flexibility and reliability — plus lower power consumption than hydraulic machines, and easy programming.
The eP 1336 uses a pulley belt system powered by servo drives that distributes the bending force over the whole bending length of the beam (the system has fixed and moving rolls spread out over the total working length of the upper beam). The belt is reinforced with steel wire and is maintenance-free.
Moreover, its function is not based on friction but on tension; and thermal influences on precision are eliminated through the absence of oil associated with hydraulic systems. Also contributing to accuracy is the use of a rigid ‘O’ frame that ensures tool alignment — even under stress deformation — as there is no horizontal displacement.
Furthermore, the position of the upper beam in relation to the lower beam is measured by dual Y1 and Y2 linear encoders that are independent of the machine frame.
This design isolates ram positioning accuracy from any deflection in the side frames under load and maintains accurate positioning — even during off-centre bending operations. Prima Power says ram repeatability on its eP-series press brakes is ±0.005mm.
Control is via Prima Power’s Electro Open Control, a Windows-based system with two processors — one for real-time operations and one for bending applications.
Also featured are a 17in touch-screen user interface that is designed to minimise programming time, while 2-D graphical programming with automatic bending sequencing maximises operator productivity.
Furthermore, the control can be upgraded to accommodate 3-D off-line programming and 3-D visualisation via the AutoPOL off-line programming system.
This offers advanced bending simulation, making it possible to shorten set-up times and ensure that the bending task can be performed. Furthermore, 3-D models can be created with AutoPOL’s designer facility; they can also be imported in 2-D and 3-D format from most CAD programs.
AutoPOL’s bend allowance algorithm takes account of bending-tool radii to ensure that the correct unfolding dimensions are used (the 2-D unfolded pattern can be exported as a DXF file to be used in programming punching and cutting machines).
Dan McGinty, Prima Power’s general manager (sales UK and Ireland), says: “The eP press brakes offer high rates of acceleration and deceleration; compared with hydraulic machines, reductions in cycle times of 30% or more are achievable.
“The working speed is programmable to ensure that bends are made without loss of product quality or operator safety, while the Lazer Safe system provides safe high-speed closing to within 2mm of the forming-cycle start position, saving up to two or more seconds per cycle.”