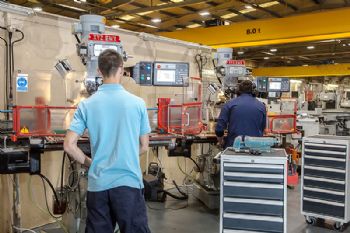
Bisley started as a one-man business in 1931, with founder Freddy Brown using his sheet-metal skills to repair damaged cars; it has since developed into a leading designer and manufacturer of steel-based storage units for offices and workshops.
The company’s manufacturing is now concentrated at its factory in Newport, Wales, where 60,000m
2 of floor-space on a 17-acre site houses manufacturing technology worth some £80 million; this includes the heavy presses, punch presses, press brakes, lasers, roll forming machinery and paint systems required to make over 20,000 units a week.
All of this manufacturing is undertaken according to the principles of ‘lean manufacturing’ and kanban, so keeping production flowing efficiently is vital.
This is why Bisley has always operated its own toolroom, as doing so ensures the timely availability of new tools and prompt tool maintenance.
With the tool-room key to continuous production, the decision was taken towards the end of 2016 to replace some old and increasingly unreliable machinery.
Bisley’s John Hancock said: “With the machines we had, we were always chasing accuracy; in an environment such as this, that is time-consuming. As a result, we decided to upgrade our existing milling and grinding sections — and add some EDM capacity.”
About 50% of Bisley’s budget for the upgrade was allocated to additional milling, turning and grinding capacity — all supplied by Burlescombe-based XYZ Machine Tools (
www.xyz machinetools.com).
The new machines are an SMX 3500 ProtoTrak bed mill, two EMX turret mills, an SLX 355 ProTurn lathe, two 1632 surface grinders and a 1224 surface grinder (all three grinders feature incremental down-feed).
These machines are in addition to an existing SMX 5000 bed mill that was transferred from the tool-room at Bisley’s former Surrey location.
Known quantity
Mr Hancock said: “Our previous experience with the SMX 5000 was instrumental in our choice of XYZ for mills and lathe, particularly as the ProtoTrak control has all the functionality that we need, is reliable and offers value for money.
With the new SMX mills we are seeing improved efficiency due to their versatility; moreover, we can machine parts and features that would have been very difficult — if not impossible — before.
Features such as TraKing, which allows us to manually work through a program prior to going full CNC, is very useful, while the control’s ease of use makes the whole machining process straightforward.”
The Bisley tool-room is home to nine tool-makers (including three apprentices). Only two of them had prior experience of the ProtoTrak control, but after a short training session at XYZ’s headquarters, all were happy to program and operate the SMX and SLX machines; more-advanced training will be carried out on-site at Bisley, as and when required.
Richard Warwick, Bisley’s tool-room section leader said: “The combination of the support we had and the straightforward nature of the control system is allowing us to machine mainly one-off parts to tight tolerances on rapid turn-round.
“The XYZ machine range also met our grinding requirements, particularly as there was no comparison between size and cost of these machines and the ones we had been using.
“Most of the grinding work we undertake is producing flat surfaces, with some occasional profiling required.
“In terms of value for money, we bought the two largest XYZ grinders for the price we would have paid to replace just one of our existing machines of the same make. Adding the third, smaller machine then became a simple decision.
“The end result is that we now have the tool-room capacity we need to keep the production side of the business running smoothly.”