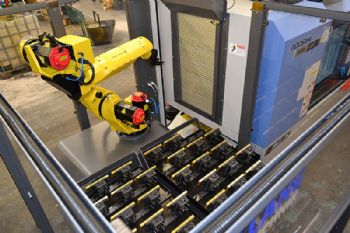
While equipment such as bar-feed mechanisms has for some years enabled businesses involved in turning operations to work ‘lights out’, automation aids such as the Lang Robo-Trex system from Aylesbury-based Thame Workholding are allowing businesses such as Qualiturn Products to operate machining centres unmanned for extended periods.
Based in Hertford and founded in 1974, this company is now one of the UK’s leading suppliers of precision mill-turned components.
In 1990, it became one of the first UK sub-contractors to instigate an unmanned mill-turn machining regime throughout each night shift; since then, it has operated 24hr a day, seven days a week, 365 days a year with only day-time staffing.
Now run by second-generation managing director Nick Groom, Qualiturn established Qualimill in 2014 — a sub-contract milling division that embraces the company’s successful ‘lights out’ operating methods (
www.thameworkholding.com).
Substantial investments in the latest machining centres and automation have resulted in Qualimill becoming an extremely successful sub-contract manufacturer of milled components.
The Lang Robo-Trex robot system that the company installed feeds a Doosan DNM500 machining centre from two trollies.
These serve as mobile storage mediums for multiple vices that hold workpieces ready to be loaded into the machine; and depending on the part sizes involved, each trolley can store up to 42 loaded vices.
The Lang Robo-Trex system, which uses an articulated robot with a handling gripper, can handle workpieces weighing up to 12kg.

Fed by this system, the Doosan machining centre runs throughout the day shift, using trollies that have been pre-loaded with parts in an area away from the machining centre.
Following a machine cycle, each finished part is returned to a trolley; and when the trolley is full, it is simply wheeled away and replaced by one loaded with workpieces.
Before the end of day-time production, the Robo-Trex trollies are replenished with workpieces, thereby enabling the Doosan machining centre to run throughout the night.
Robo-Trex trollies are available in two sizes. The first accommodates 30 vices with a maximum part size of 120 x 120 x 100mm, while the second accommodates 42 vices with a maximum part size of 120 x 100 x 70mm.
The system can handle four automation trolleys; this means that — depending on part size — the available storage capacity is either 120 or 168 vices.
The patented edgewise mounting of the system’s vices ensures maximum space utilisation, while good accessibility to the clamping device allows workpieces to be exchanged without removing the vice; and because external access
to the trolley is possible, production remains seamless, as machining cycles do not need to be interrupted.
Control of the zero-point clamping system can be performed either pneumatically through the machine tool or mechanically through the system’s robot.
Explaining the reason for purchasing the Robo-Trex system, Mr Groom said: “To help accommodate the rising demand for our milling work, we recently considered purchasing another machining centre, but recognising the success of the unmanned operating methods we use for our mill-turn operations, we investigated equipment that would allow efficient ‘lights out’ running of an existing CNC machine.
“We found the ideal answer in the Lang Robo-Trex and subsequently became the first company in the UK to install one of these systems, having calculated that this would be more cost-effective than buying another machine. Moreover, the effectiveness of the Robo-Trex is such that we already have plans to install a second system.”