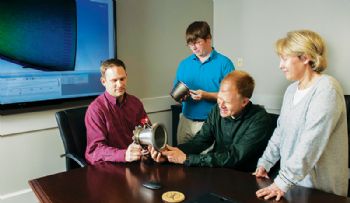
Due to the combustion process, rocket-engine nozzles operate in extreme temperatures and pressures. Moreover, they are typically complex and costly to manufacture.
For these reasons, a team of engineers at NASA’s Marshall Space Flight Centre in Huntsville, Alabama, (
www.nasa.gov) set about developing and proving out a new additive-manufacturing technique for nozzle fabrication.
A new process called Laser Wire Direct Closeout (LWDC) has been developed to build a less-costly nozzle — in significantly less time. LWDC differs from most 3-D printing technologies, which are powder-based and see the part fabricated in layers.
It uses a freeform-directed energy wire deposition process to fabricate material in place. This new NASA-patented technology has the potential to reduce the build time from months to weeks.
Nozzles may look simple from the outside, but they are in fact highly complex. The LWDC method precisely closes out (seals) the nozzle coolant channels, which contain the high-pressure coolant fluid that protects the walls from high
temperatures.
Paul Gradl, senior propulsion engineer at Marshall’s Engine Components Development & Technology branch, said: “Our motivation behind this technology was to develop a robust process that eliminates several steps in the traditional manufacturing process.
“The process is complicated by the fact that the hot wall of the nozzle is only the thickness of a few sheets of paper buy must withstand high temperatures and strains during operation.”