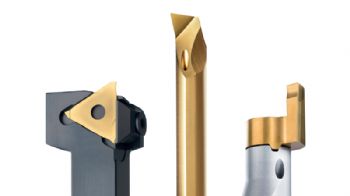
Materials that are difficult to machine can present significant challenges to cutting tools, particularly when it comes to small and miniature parts.
To better serve these applications, Ringwood-based Horn Cutting Tools Ltd (
www.phorn.co.uk) has made available the EG3 and EG5 coatings for its Supermini product series, which is suitable for the boring and grooving of holes upwards from 0.2mm in diameter.
The distinction between the two types of coating rests in their substrates and layer thickness. According to Horn, the coatings are extremely smooth, so they have low friction; this reduces the amount of heat transferred to the tool, especially the cutting edge.
Numerous in-house tests — along with feedback from customers — confirm that the coatings can double tool life (depending on the material). Horn’s EG3 and EG5 coatings are also suitable for the Mini and 312 tool systems.
In another development, Horn’s milling tools based on Boehlerit products have been expanded to include the ETAtec 45P face-milling cutter (pictured) and ZETAtec 90N roughing mill.
ETAtec 45P milling cutters, with diameters from 50 to 160mm, have between five and 10 seven-edged inserts. Moreover, they not only offer a 45deg approach angle and positive geometry but also generate low cutting forces, thereby
ensuring smooth machining coupled with high levels of productivity.
The multi-functional concept involving one tool-holder for two different insert versions means that the inserts designed for face milling can be swapped for round cutting inserts if — for example — profile milling needs to be performed.
Horn says ETAtec 45P cutters really show their capabilities in applications involving long-chipping materials, such as stainless steels, titanium or nickel-based alloys. For these materials, inserts with or without chip-breaker geometry — and in various steel grades — are available.
ZETAtec 90N cutters with diameters from 50 to 160mm feature five-10 inserts, each of which has six cutting edges. The high reliability they achieve during roughing is due to their negative geometry, while the positive rake angle facilitates a smooth cut.
These cutters can be used for helical or linear plunging, despite their negative geometry.
The benefits of the cutting insert's properties are particularly apparent in applications where short-chipping materials are being machined.
To ensure that the correct cutting insert is available for the task, two substrates and geometries are offered: one grade for stainless steels and one for cast and non-ferrous metals.