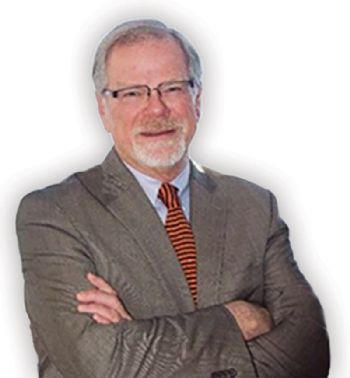
The Utah Advanced Materials & Manufacturing Initiative (UAMMI) (
www.uammi.org) recently announced that it has been awarded nearly $1 million in federal funds to produce carbon composite additively manufactured (AM) parts for the US Air Force.
AM technology will allow UAMMI to 3-D print carbon-based replacement parts for legacy aircraft on demand — these parts are often prohibitively expensive using traditional techniques.
UAMMI’s award comprises a two-year $928,000 project that will begin in June; the funds will come from the USAF’s MAMLS programme (Maturation of Advanced Manufacturing for Low-Cost Sustainment), which was created in partnership with the Air Force Research Lab, National Center for Defense Manufacturing and Machining, and America Makes.
As a non-profit initiative, UAMMI’s role is to ensure that Utah is the global leader in value-added advanced materials, manufacturing, technology development, and design.
UAMMI says being awarded this funding will allow it to bring the 3-D printing of carbon materials to the forefront in Utah.
Jeff Edwards, UAMMI executive director (pictured), said: “Additive manufacturing represents a huge opportunity for Utah’s advanced manufacturing industry.
“The carbon-based components we will produce will be highly valuable to the Air Force, as they will significantly reduce both the time and cost of aircraft repairs.
“This grant will help position Utah as the technology leader and innovator in this new field.”
As aircraft age, the availability of parts for repairs gets increasingly difficult, and waiting for replacement parts to be made using traditional fabrication methods is a significant cause of maintenance down-time.
Via MAMLS, the Air Force intends to demonstrate that, with current advances in additive manufacturing, these parts can be made on demand using composite-based additive manufacturing (CBAM) technology and to “build a body of CBAM knowledge for today’s non-critical part replacements”.
Non-critical parts of interest include electrical connectors, instrumentation knobs, wiring harnesses and small brackets.