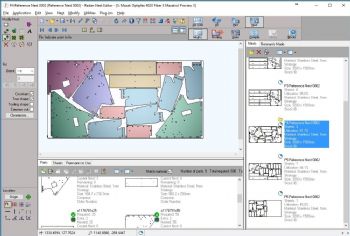
The 2018 R2 release of sheet-metal software Radan (
www.radan.com) includes newly developed features that give users a greater degree of manual control whenever flexibility is required for certain aspects of their production processes.
The company says that while full automation is ideal for simple parts and plays an important role in manufacturing complex components, there is often the need for some complementary manual input.
As a result, it has added several more-focused tools that allow users to better control this requirement.
One such tool is Grid Nesting, which gives additional flexibility for users wanting to create or manipulate a nest manually.
For example, if a sheet is not completely full, users can either let the automatic nester take over or, if they have a clear idea of what is required, use Grid Nesting to provide an easy way of filling a space with a particular part; they can even stipulate the component nesting direction.
The previous version allowed users to manipulate automation to get the required result, but Grid Nesting achieves
it much faster.
Reverse Cutting Direction is another example of providing additional user control, and it is particularly important for CNC plasma cutters. The plasma cutting of thicker material often generates considerable heat, which can cause the metal to distort.
This issue can now be resolved with a single mouse click to simply reverse the cutting direction on certain areas of the material, where heat might be problematic.
Moving on to new automation functions, one major update is an improved way of calculating the most effective remnants.
Previously, the operator had to manually choose the shape of the remnant — square or rectangle — but the Improved Remnant Handling function ensures that the best-possible option is always cut.
Another newly developed function, Picker Arm Movement, provides additional automation on the machine tool.
Automated systems that manipulate the part after it is cut are becoming increasingly popular, even for large complex components; Radan now automatically predicts the best way to handle the part, so the operator does not have to make that decision.
Continuing the automation theme, a single click in Radan 2018 R2 now creates a detailed production pack for all nests.
Every NC program traditionally comes with an instruction sheet for the shopfloor, and providing this was traditionally a manual process for each individual nest.
Now, one mouse click introduces additional information into the pack, which is produced automatically for any number of nests.
As some jobs could contain up to 50 nests or more, this is a major time-saver.
A new set of automation options in Radbend for press brakes means that templates can be created to specify steps that previously had to be set up manually.
In addition, the DIN Unfolding function enhances the way a part is unfolded in Radbend, placing more emphasis on the
designer’s intentions — particularly regarding the importance of the radius.
With regard to the Radm-ax module for tube cutting, Vero says that the Common Cutting for Tubes function is an important enhancement.
Separating tubes by just one cut, instead of cutting the end of each tube individually, improves efficiency, especially on thick complex parts with large diameters.
Finally, a number of updates to Radan’s Logistics suite include giving users three different options on how they calculate the cost of material required to make an individual part; also new is the ability to mark purchased items on the complete assembly drawing, plus the cost per piece, so they can be included in customer quotes.