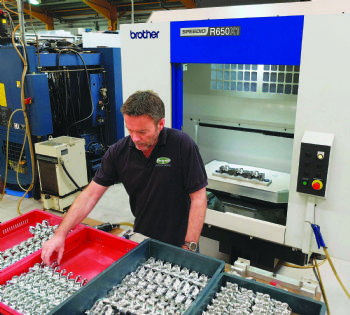
At the Barnoldswick factory of bicycle after-market component manufacturer Hope Technology, nearly all parts are machined from aluminium; and due to the relatively light metal cutting involved, it is not surprising that ‘nimble’ 30-taper machining centres are found on the shopfloor — alongside more powerful but ‘relatively ponderous’ 40-taper machines.
Works and production manager Lindley Pate has started to replace some 40-taper machines with 30-taper technology.
Highlighting this change was the installation earlier this year of a Japanese-built Brother R650X1 30-taper three-axis vertical machining centre (VMC) with a work envelope of 650 x 400 x 305mm and twin pallet changer (2APC).
Supplied by Kenilworth-based Whitehouse Machine Tools Ltd (
www.wmtcnc.com), it replaced an ageing 40-taper VMC/2APC model with a similar working envelope.
The resulting benefits have been significant. For a start, the Brother machine is much more productive, completing Op2 on three twin-piston brake calipers (fixtured side by side) in 19min — a 40% reduction on the previous time of 32min.
Indeed, Mr Lindley says that time savings of this order are typical for the expanding range of parts being transferred to the 30-taper machine.
Furthermore, the footprint of the R650X1 is 20% smaller, which is helpful in a busy factory requiring ever more machine tools to service a percentage increase in turnover that is well into double figures annually.
Power-efficient
A third advantage is that a 30-taper machining centre draws less power than a 40-taper machine with an equivalent working envelope, so there is an on-going reduction in energy consumption.
Furthermore, the R650X1 provides regenerative power from spindle deceleration, while the Brother CNC-C00 control minimises the power consumed by motors, pumps and lights by putting them into standby mode when not in use.
Mr Pate said: “We use 10 machining centres with 30-taper spindles and 15 with 40-taper spindles — a mix of VMCs and horizontal-spindle machines.
“Half of the 40-taper machines are in multi-pallet cells, and that will not change. In fact, at MACH 2018 I ordered another five-axis model with a 32-pallet pool.
“Our single-table stand-alone 2APC 40-taper machines offer the greatest scope for being swapped with a 30-taper machine.
“The benefits are compelling, due to the higher output that is possible using the smaller tool interface — plus the accuracy and repeatability are just as good.
“In fact, on the latest Brother machine, we hold 5µm total tolerance on some components such as cassettes, which have to mate with another sprocket set produced on a different machine to provide the higher gear ratios.

“Moreover, the face-and-taper contact with the tool’s back end offered by BIG Plus spindle on the latest R650X1 ensures extreme rigidity and allows — for instance — a 32mm-diameter face mill to skim components to achieve a fine finish on cosmetic features.”
Hope’s first purchase from Whitehouse Machine Tools was five years ago, when it bought two 30-taper Brother TC-2RB three-axis machining centres to cope with a growing workload.
At the time, Hope was using — and it still does — six 30-taper machining centres of a different make, some equipped with manual pallet change.
The TC-2RB machines were selected for their higher speed and the compact design of the automatic pallet changer.
Brother calls this a QT (quick turn) table; it is essentially one large pallet rotating around its centre, so no time is lost by having to temporarily disengage pallets for 180deg indexing into and out of the machine’s working area.
Increasing demand
The first R650X1 was installed at Barnoldswick two years ago, again to cope with steeply increasing demand for Hope bicycle accessories.
The machine was considerably faster in-cut than the TC-R2Bs; it also provided a larger table — 800 x 600mm instead of 600 x 300mm — and at a competitive price.
The extra table area allows more parts to be fixtured for longer run times (this is especially useful for ‘lights out’ machining during 24hr operation, currently from Monday through to Thursday; a single shift is operated on Friday, and weekend working is according to demand).
Further benefits of the R650X1 are the option of 22-tool storage capacity (rather than 14 positions on the TC-R2B), 15-bar coolant delivery through the 16,000rev/min spindle, and 30m/min cutting feed rate in all axes (on the TC-R2B the feed rates are 10m/min in X and Y and 20m/min in Z).
The inherent speed of all Brother machining centres derives from fast tool change and APC times, as well as 50m/min rapids — all happening at the same time, so that the tool is in position to cut the next part immediately after pallet change-over.
Moreover, the large memory capacity in the Brother control allows two dissimilar Hope parts to be fixtured and machined on the R650X1’s pallets; on older 40-taper machines, a relatively complex part had to be machined two at a time due to insufficient control memory.
The ability to produce different parts on one machine is useful to Mr Pate, who sees many new component derivatives arriving all the time from the design office, but very few being deleted.
In conclusion, Mr Pate said: “There is a greater variety of 30-taper milling centres around now, and more tooling is available to use on them. They are extremely compact, helped by the carousel style of tool magazine.
“We use two makes of 30-taper machine here, and in my opinion, the Brother machines have the edge in terms of speed, compactness and value for money; they also provide good access for loading and unloading, so they are popular with our operators.”