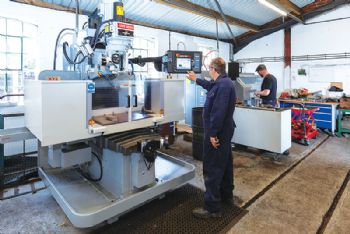
Built in 1903, the Welshpool and Llanfair Light Railway served the communities along a winding valley and joined the mainline at Welshpool. This narrow-gauge railway allowed livestock, coal and timber to be transported; it also provided a passenger service until the early 1930s.
The line operated until 1956, when British Rail deemed it uneconomic, but a regular steam-hauled public service returned to the line in 1963, after a group of enthusiasts took on the challenge of making it into a successful tourist attraction.
Key to that success was the retention of two of the original locomotives, along with the acquisition of rolling stock from railways in the UK and Europe.
These engines and carriages require regular maintenance and care, which is where the railway’s engineering workshop comes into play.
The first maintenance workshop was built in 1968, and the locomotives lived outside in the elements until 2000. An extension to the workshop in the 1980s saw the development of the machine shop, with machine tools being ‘begged or borrowed’ from supporters of the railway.
Matters improved in the 1990s, when a Heritage Lottery grant allowed some additional machines to be purchased — and more so when mechanical engineering manager Richard Featherstone joined the railway in 2016.
He said: “We had a lot of manual machines. Making parts on them was time-consuming, and given that we rely on skilled volunteer labour, time is at a premium. We needed a bigger and faster milling and turning capacity that was user-friendly.”
Following an appeal for funds, the workshop was able to buy two machines from Burlescombe-based XYZ Machine Tools (
www.xyz machinetools.com) — an SMX 4000 bed mill and an SLX 425 ProTurn lathe, both with the ProtoTrak control.
These machines made an immediate impact on the way that Mr Featherstone was able to undertake maintenance of the engines. One example was spark arrester plates for the smoke-boxes, which are made up of a sandwich of stainless-steel plates and mesh held in place by 28 M6 screws.
“Historically, these M6 drilled and tapped holes would have been marked out, centre-popped and manually drilled, then adjusted by the fitters on assembly. We now machine them on the SMX 4000; and with every hole in the right place, the time savings for assembly are significant.”
Similarly, the SLX 425 ProTurn lathe is generating major benefits for Mr Featherstone and his team of volunteers. Each of the couplings between engines and carriages has an adjusting nut with a 11/4-4TPI round thread form.

A batch of 15 has been manufactured by a semi-skilled volunteer in an afternoon on the SLX 425; using manual machines, this was a week’s work.
For traceability, these parts are then put on the SMX 4000 and etched with the relevant details; previously, this would have been done by hand with letter and number punches.
“Maintenance and refurbishment is a continuous process here, as the engines and components are subject to an aggressive environment — we are either boiling things or burning things.
“For example, after every 28 days of an engine ‘being under steam’, we have to replace/re-work the two fusible bronze plugs in each boiler; these act as a failsafe if water levels drop.
“Making these plugs was a ‘black art’, as they feature a taper thread that must be both accurate and a specific length; four complete threads should be showing on the inside of the firebox — a situation complicated by the fact that the female thread is re-tapped and opened up occasionally.
“It is now a straightforward procedure, as I can call up the program on the ProtoTrak control on the SLX 425, adjust the offsets and be confident that we will produce accurate parts first time.
“It used to take a skilled man 4hr to produce two of these fusible plugs manually; we can now turn them in just 15min.”
Programming is currently done at the machine by Mr Featherstone; he is then happy to hand over operation of the machines to semi-skilled volunteers.
One feature of the SLX lathe that he highlights is the TraKing facility, which allows him to use the handles to move through a program while remaining in full control.
“With this feature, you can back off if you have any uncertainty about the tool-path. That said, the ProtoTrak control is so easy to use; and with step-by-step instructions it is easy to get things right first time.”
Battle bots
For followers of the BBC’s Robot Wars programme, the names Sir Killalot, Shunt, Matilda and Dead Metal will be familiar as the ‘house robots’, whose sole purpose is to lie in wait for the competing bots and take their opportunity to destroy them.
These ‘weapons’ are designed and built by two brothers in a small corner of their family business — one that is more used to manufacturing furniture castors.
Grant and James Cooper both worked for the Birmingham-based family company Priory Castor and Engineering, but as the demands on that business changed, they saw a need to diversify.
The result was Robo Challenge, a design and creative engineering business that works alongside TV production companies to create one-off robots and engineering concepts.
Grant Cooper said: “Our role is to deliver on other people’s ideas, usually in a very short time-frame. The production company will approach us with an idea, which we then bring to life.”
One example of this was the Robot Wars house robots, which had to be more powerful and destructive than anything the competitors could dream up.

Although the brothers were not allowed to compete in the BBC’s Robot Wars, they built a robot called Spectre and took it around the world, competing in TV series.
They were declared World Champions after competing in China’s King of Bots series.
To achieve this level of success, the bots have to be engineered to the highest standard; Robo Challenge uses an XYZ LPM vertical machining centre to create a wide range of parts from aluminium, titanium and stainless steel.
The machine is worked hard; not only are parts made from some ‘difficult materials’, they are often wanted very quickly. “We tend to be at the end of the process; after weeks — if not months — of discussion have taken place, we are asked to produce complex machines in a short space of time.
“For example, the four house robots for Robot Wars were designed and built in less than eight weeks. Typically, we get one to three weeks to complete a project, so an efficient machine that can be used by anyone here was essential for us.
“The LPM — with its ProtoTrak control, tool changer and large table — works perfectly for us, especially as just about everything we produce is a one-off.”
The versatility of the ProtoTrak PMX control allows Robo Challenge to either program at the machine using the straightforward conversational programming system or download post-processed files straight from its Autodesk Fusion 360 CAD/CAM system.
The company also works with its tooling partner Guhring (a sponsor of the brothers’ robot activities), so as to push tooling as hard as possible and the capability of the machine tool.
In conclusion, Grant Cooper says: “We are not CNC machinists; our background with the family business is pressing and assembly, so to have such an easy machine and control system to work with is a major advantage, especially given the time-frames that we have to work to.”