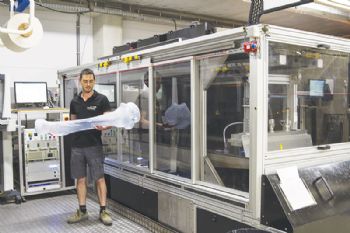
Materialise NV is undertaking its largest stereo-lithography project yet — a life-size 3-D printed reconstruction of the first mammoth skeleton ever displayed in Western Europe (
www.materialise.com).
The 320 bones making up the skeleton were scanned and will be printed, finished and fitted together.
From October onwards, the 3-D printed mammoth will be on display in the Belgian city of Lier, where the original mammoth was found.
Since 1869, the Mammoth of Lier has been on display at the Royal Belgian Institute of Natural Sciences in Brussels.
Almost 150 years later, it is returning to its roots in Lier — albeit in a significantly more modern form. The entire skeleton will be 3-D printed by Materialise (in close collaboration with the museum in Brussels) and mounted on a ‘quasi-invisible’ frame.
Reconstructing the mammoth presented a significant challenge for the Materialise engineers. Every one of its 320 bones was scanned at the museum in Brussels, and the skeleton was digitally reconstructed in close collaboration with the resident paleontologist to achieve the highest-possible degree of anatomical accuracy.
Each scan also needed to be cleaned up and prepared for the 3D printer with Materialise Magics software, since a scan simply produces a 3-D image instead of a structurally sound 3-D form that is suitable for 3-D printing.
Instead of using the original 19th-century exterior mounting system, a more-advanced interior mounting structure made of carbon will be created and integrated inside the plastic bones; this meant that in the digital phase, Materialise engineers already had to think about how to fit the structure within the bones, integrating entry and exit holes in them for the carbon tubes.
For the modular carbon structure, Materialise worked with its daughter company RapidFit to design a sturdy and lightweight system (weighing just 300kg).
The bones are being printed on nine of the aptly named Mammoth stereolithography printers at Materialise, which were specially designed by the company for projects that require extra-large printer capacity.
However, applying 0.1mm of resin at a time, the mam-moth will take more than a month to print, before being finished and given a combination of different paints, textures and lacquers so that the bones match the original skeleton as closely as possible.