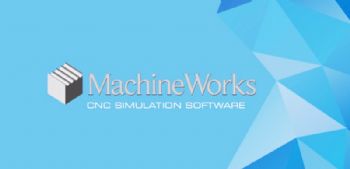
The 2.2 release of the Polygonica mesh modelling software tool-kit — available from Sheffield-based Machine Works Ltd (
www.machineworks.com) and recently demonstrated at the TCT Show in Birmingham — includes significant upgrades
to the ‘point-cloud to mesh’ processing ‘pipeline’, thereby allowing CAD, CAM and CAE vendors to easily integrate advanced point-cloud import capability directly into their existing software systems for the direct support of scan-based work-flows without the need for external software.
Meanwhile, a new surface-fitting method initially builds a surface-based structure from the point cloud, and the mesh is then generated from that. This technique gives much smoother mesh surfaces for ‘noisy’ point data that are more suitable as a starting point for reverse engineering.
Polygonica’s hole-filling algorithms have also been upgraded. For example, ‘annular hole-filling’ automatically recognises islands and attaches them to the correct hole, while ‘ruled-surface filling’ joins a hole with a single island using a ruled surface. This can also be used to “bind disjoint sheets”.
Furthermore, the ‘features’ method “respects features across a hole in one direction”, while the ‘features smooth’ method recognises features in all directions and “creates a smooth surface that respects the curvature at the hole’s edges”.
Indeed, Polygonica’s new automatic hole filling allows multiple holes to be filled in at once, greatly improving the software’s performance for large meshes — and hole boundaries can be automatically smoothed during post-processing.
A new offsetting method has been added that allows simultaneous inwards and outwards offsetting in one operation — and open surfaces can now be extended for improved trimming.
In addition, ‘adaptive simplification’ algorithms in Polygonica are now multi-threaded, so large meshes from laser scans can be processed in seconds while maintaining the appropriate tolerances.
A new ‘shrink wrapping’ function has also been added; this closes very-poor-quality meshes and ‘triangle soups’ while removing internals from CAD assemblies to reduce data for faster visualisation in virtual-reality/augmented-reality and mixed-reality scenarios.