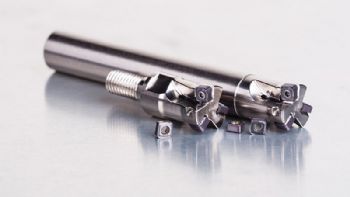
The family of ‘economical milling tools’ available from Chesterfield-based Dormer Pramet (
www.dormerpramet.com) has been enhanced by several new ranges for semi-finishing and finishing in die and mould machining applications.
Featured are various CNHX05 double-sided inserts with up to four cutting edges and patented wiper edges that produce a high-quality surface finish and result in reduced machining time in both shoulder-milling and face-milling applications.
These inserts are complemented by a range of SCN05C cutters for the productive copy milling of steels, hardened steels and cast irons.
Available in diameters from 12 to 20mm, the tools have a close pitch that allows a productivity that is at least 20% greater than that achieved by standard-pitch cutters when undertaking contouring, profiling, plunging and face-milling applications; these tools have also been optimised for the smooth cutting of corners and pockets.
Meanwhile, Dormer Pramet has launched the double-sided WNHX04, an insert with six cutting edges and a patented wiper edge designed to generate a “superior finish on component walls and faces”, while reducing the time in cut.
This latest insert is compatible with a new range of copy milling tools; SWN04C cutters are available in diameters from 20 to 35mm and with a variety of differential-pitch options.
Designed for smooth cutting in operations with long overhangs, these cutters can be used for contouring, profiling, plunging and face-milling applications with depths of cut up to 2mm; and as with SCN05C cutters, the SWN04C range is suitable for semi-finishing and finishing applications in steels, hardened steels and cast irons for the mould and die sector.
In a recent example, the WNHX insert with WM geometry and the new M4310 grade was used to machine tool steel at a 0.50mm depth of cut, a cutting speed of 196m/min and a feed rate of 3,600mm/min — reducing machining time by 45% compared to a competitor’s ‘equivalent’ tool.