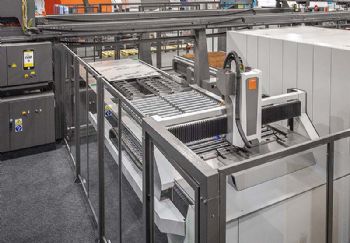
At the recent
EuroBLECH exhibition in Hannover, Bystronic (
www.bystronic.com) showed new solutions that in the near future will enable the Swiss company’s automated Production Line for end-to-end manufacture of sheet metal parts to be expanded with modules for pre-processing components.
For example, before laser cutting the parts, the new ByFlex system can drill holes as well as deburr, thread-cut and countersink them.
In addition, a labelling function marks the parts with a code that can be scanned at downstream stations. Also launched was new software architecture, called Shop Floor Control System, for monitoring and controlling a complex production facility, which might involve an automated manufacturing solution such as Production Line networked with stand-alone sheet metal handling and machining stations — including those from third-party suppliers.
The software assumes the centralised control function and helps users to optimise production flow continuously. Within Shop Floor Control System, each integrated element provides real-time information on the current order status, scheduled maintenance and updates, or on any malfunctions.
The heart of Production Line is a Bystronic 10kW ByStar Fiber 3015 laser cutting machine in which the cutting head (developed in-house) adapts the focal point of the laser beam to match the sheet thickness and type of material. In this way, quality is maintained even if the sheet thickness varies.
Steel, stainless steel, aluminium and non-ferrous metals such as copper and brass in gauges from 0.8 to 25mm can be processed.
ByVision Cutting control software, which has been designed to allow even novice operators to master the machine rapidly, supports the user with a database of parameters for different sheet metal types and cutting technologies.
Another core component of the line is the ByTrans Cross loading and unloading automation, which is connected to the fibre laser cutting centre and to a material storage tower (the latter ensures the supply of raw metal sheets and the removal of parts and skeletons to and from the laser’s shuttle table; it also accommodates finished cut parts and skeletons).
To make unloading the laser even more flexible, Bystronic offers a BySort module that deposits finished components onto unloading positions next to the laser cutting system, ready for transfer to the next production process.