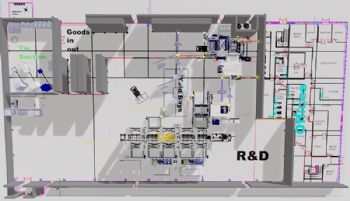
With just weeks to go before vital equipment was installed in its new factory building, Leeds-based ACS Stainless used the AMRC’s Virtual Reality (VR) expertise to show its staff what their new workplace would look and get some feedback on the proposed layout.
Jake Senior, digital software engineer at the AMRC’s Integrated Manufacturing Group (
www.amrc.co.uk), said: “ACS was just weeks away from starting to install a number of very large machines — some of them over 8m high — and it only had one opportunity to get everything in the right place.
“The company approached us, as it wanted to be able to validate the layout of the equipment in a visual and contextual manner; we managed to do this using VR in a relatively short time-frame.
“We used a piece of software called Visionary Render to import the CAD files of the machines and then put them in the right place by overlaying architectural drawings onto the floor plan.”
This allowed ACS staff to walk around a digital representation of the factory, using an HTC Vive headset.
David Flannery, managing director of ACS (
www.acsstainless.co.uk), said: “As with most construction projects, there were numerous changes to the internal layout of the building, as the design developed.
"Some were of our own making, but others were dictated by the various contractors that we employed on the project.
"Much of the equipment is bespoke, and it involved machine suppliers and contractors working together for the first time, so many of the challenges of altering machine layouts — and the consequences — were not immediately obvious.”
ACS was able to check whether there was enough space between machines for fork-lift access and behind them for maintenance purposes.
It decided to move some machines away from walls, make some alterations to welding bays and include a stairwell that was not part of the original plan.