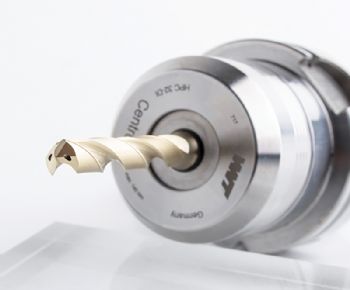
Materials such as titanium, Inconel, VA stainless, Hastelloy and Hardox pose significant challenges for machining technicians, machines and tools; as they become more common, overcoming the challenges they pose will help companies to remain competitive.
To assist its customers, Sheffield-based Ceratizit Group (
www.ceratizit.com) is investing heavily in R&D to find innovative ways to tackle the problem.
The outstanding tensile strength of difficult-to-machine materials places significant demands on the tool — particularly when machining titanium, which features low thermal conductivity and high tensile strength.
This means tools are subject to extremely high thermal and mechanical stress, making them prone to a high level of wear. In addition, the cutting edges are subject to high loads, as machining results in high cutting forces — especially during drilling.
Therefore, tools with coatings that have a high degree of elevated-temperature hardness and thermal resistance lend themselves to this type of machining.
The WTX-Ti high-performance drill from Ceratizit is one such example, developed in response to changes in the materials market; it is designed to offer high performance on difficult-to-machine materials, such as high-strength and acid-resistant steels, titanium or heat-resistant super-alloys.
Felix Meggle, product manager for drills at Ceratizit, said: “It was important for us to produce a high-performance drill that could be used with more than just titanium and Inconel.
“During development, we focused on ensuring that the WTX-Ti also delivers top-quality results when machining austenitic and martensitic stainless steels and Hastelloy.
“When machining heat-resistant super-alloys, the temperature at the cutting edge is very high, and the materials are very abrasive. The tool must therefore cut very smoothly and be incredibly stable in order to ensure a long service life.”
He pointed out that VA-type drills (designed for stainless) had frequently been used in the past — for example, to machine Inconel — as they are very sharp.
However, this is not an ideal solution, as the heat and high abrasiveness quickly lead to edge breakages on the tool. In order to reduce this wear, some innovations have been made with the WTX-Ti.
A microgeometry with protective edge rounding has been used to create a very sharp yet very stable cutting edge, able to withstand high loads.
The polished flutes of the WTX-Ti ensure safe chip removal and less chip friction in the chip chamber, therefore reducing the temperature. Out of all these measures the most important one was the coating.
Mr Meggle said: “Thanks to the latest generation of Dragonskin coating, the WTX-Ti is particularly wear-resistant and is ideally suited to the process, due to its high thermal resistance and its extremely smooth surface.”
The WTX-Ti has been subject to a variety of tests since its release.
“For example, in an internal test with austenitic steel, we reached a tool life of more than 72m. That’s huge,” points out Mr Meggle.