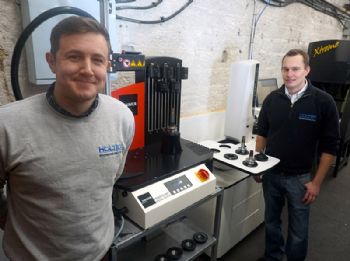
West Yorkshire-based Holtex Engineering Solutions, an ISO 9001/2008 precision engineering company, prides itself on providing a high-quality prototype and small-quantity production service with the shortest-possible lead times.
It achieves this by using the latest technology, machinery and supplier management techniques at its Holmfirth facility.
Holtex director Ben Robinson (
www.holtex.eu) said: “We’ve gradually grown since we formed the business in 2014, and we now have 10 employees.
“We have an ethos of investing in new technology; this includes some of the latest multi-axis turning machines, as well as three- and five-axis milling machines.
"This technology is supported by high-quality tooling that is complemented by the Haimer Power Clamp Special Edition heat shrink system for the milling section and the Haimer UNO20/40 Microset tool pre-setter for the turning department.
“The reason we invested in this equipment — supplied by Burnley-based Haimer UK Ltd (
www.haimer.biz) — was because a lot of the jobs we do are relatively high-precision, and we are using very delicate tooling at times.
“Additionally, the machinery we have is only as good as the tooling we put in it, and the more accurate our tooling is, the better off we are from the start.”
“A lot of our smaller and more-delicate tooling means we are producing profiles that aren’t possible to measure with normal methods — a co-ordinate measuring machine would normally be needed.
However, with the Haimer system, we can accurately set diameters and check the run-out of tooling, so we can check the part before it goes to the inspection department. ‘Right first time’ results have increased considerably. In addition, the tooling is lasting considerably longer, as it is running at a much-improved accuracy and run-out.”