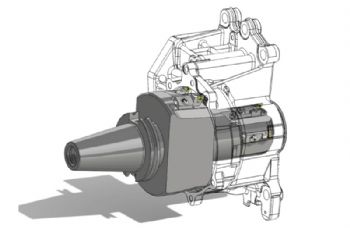
In the drive for more efficient and reliable automotive engines, machining tolerances have become ever tighter and component features more complex; moreover, just-in-time manufacturing has placed increased pressure on manufacturers to improve productivity while eliminating scrap.
A result of these demands is that single-point boring tools no longer meet the requirements of precision manufacturers, who are increasingly taking advantage of the significant performance benefits offered by combining multiple features on a single tool.
Cornwall-based Rigibore Ltd (
www.rigibore. com) uses its in-house RADS design software — in combination with decades of industry knowledge and engineering expertise — to create special tools that deliver improved part quality, cycle-time reductions and lower tooling costs; and while special tooling is seen as specific to one component (and hence costly), Rigibore says its RADS software can help design tools that are adaptable to a family of parts.
For example, for a Tier Two automotive manufacturer producing brake discs of varying width, Rigibore created a flexible solution capable of machining discs between 0.082 and 0.785in wide.
The company used a removable fixed-pocket element for facing on one side of the disk, along with a UFP (ultra-fine precision) cartridge for finishing the other face of the disc, performing both operations simultaneously.
The UFP cartridge is mounted on an adjustable slide, with a Vernier slide which the operator can use for initial settings, the fine adjustment being made by the UFP cartridge.
Taking special tools to the next level Rigibore can also integrate its Smartbore technology with non-standard tools. An example of this is provided by General Products Corp, a specialist automotive-parts manufacturer based in the USA.
The company contacted Rigibore with a requirement to replace fixed-pocket PCD boring tools, as it was experiencing a number of process capability issues.
General Products was also concerned about the significant cost and time involved in sending tools back for reconditioning when they went out of tolerance.
Combination solution
Using its Smartbore technology, Rigibore designed a combination solution with roughing and finishing inserts on the same tool, allowing multiple features to be machined in a single pass.
The use of Smartbore technology with its ‘Digital Adjuster’ meant that adjustments to the finish cartridge could be made simply, quickly and with micron accuracy, while the tool was still in the machine spindle.
To further maximise the benefit of these tools for General Products, Rigibore used PCD inserts to provide the same durability and wear-resistance as previous fixed-pocket tooling, with the added bonus of fast and simple replacement in the case of tool damage.
The result of applying Smartbore technology, which allows operators — “regardless of their skill levels and experience” — to accurately set and maintain tight tolerances, significantly reduced the cost of the overall tooling package and greatly improved part quality and consistency; it also gave a 12% reduction in cycle time, which was key to meeting productivity requirements.
The benefit of controlling every aspect of design and manufacture allows Rigibore to respond quickly to customer needs, with quotations being generated within 48hr and delivery of a finished tool within six weeks.
This level of service was vital for another automotive customer requiring an alternative to improve consistency and surface finish on bearing shaft components.
These 58HRC hardened-steel components posed challenges in terms of tool life. Rigibore used CBN inserts combined with its Active Edge automated tool-control system, which allowed for adjustment of the tool remotely, eliminating any need to access the machine or tool carousel.
This capability allowed the customer to make adjustments more frequently — and with micron accuracy — to maintain size well within tolerance, while also achieving the required surface finish.
An added benefit of achieving the improved consistency and quality of the bore was being able to eliminate the requirement for a subsequent grinding operation.
The streamlined process of boring and overturning took just 25sec.