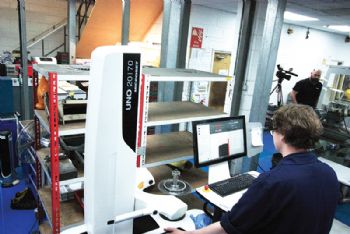
Dorset-based Allied Tooling has continually developed its cutting-tool business since it was founded almost 40 years ago; it now offers a comprehensive range of services, from the supply and sharpening of TCT saw blades to bespoke tooling — including PCD — for the metal-cutting and wood-working sectors.
The company offers leading brands of metal-cutting bandsaw blades and HSS circular saw blades, along with the re-grinding and manufacturing of engineering cutting tools, including special tools, step drills, form tools and TCT tooling.
It recently spent more than £1 million on new equipment, including Vollmer and Anca grinding machines, as well as three machines — a Tool Dynamic TD Comfort balancing machine, a UNO 20/70 Microset pre-setting machine and a Power Clamp Economic Plus NG heat-shrinking machine — from Burnley-based Haimer UK Ltd (
www.haimer.biz).
When asked why Allied opted for the Haimer pre-setting machine, engineering director Rod Knight said: “I looked at every machine on the market, but this one really suited our needs.
"It is simple to use, the software is very user-friendly, and we opted for a version with a travel height of 700mm, which would accommodate our long tools.
“The Haimer UNO is used in conjunction with our two Vollmer QXD spark erosion machines.
“We have to pre-set the tools to a specific height; and when that has been done, we can load the data from the UNO directly into the Vollmer CNC machines, which then run 24hr a day without any operator intervention.
"By pre-setting the tools, we can load them into the Vollmer loading stations, push the button and have a batch of finished PCD tools at the end of the day.”
Mr Knight added: “With the Haimer heat-shrinking system, we can now fit customers’ tools into holders for them. What we do is re-lap or re-grind tools in the holders, thereby ensuring that they are perfectly concentric.
"This has taken our business into an area that we didn’t have before — providing a complete refurbishment service for these tools.”
With regard to the Haimer tool-balancing system, Mr Knight said: “Tool balancing is very important to our business — and that of our customers.
“Everything we do on our Vollmer machines has to be balanced to within G2.5 — G being a measure of the balancing quality of a rotating body.
“This level of balance is essential, especially as some of the machines that use these tools have spindles running at more than 24,000rev/min.
“We have bought ‘balanced’ tool-holders from a number of companies, and when we put them on the Haimer balancing machine, I have been staggered by how bad some of them are.
“I bought a balanced tool-holder expecting it to be G2.5, but tests found it to be balanced to G48, which is way out for the application intended.
"Somebody buying these tool-holders probably won’t appreciate how much this degree of imbalance could affect their spindle — which is why our balancing machine is so fundamental to what we are doing.”