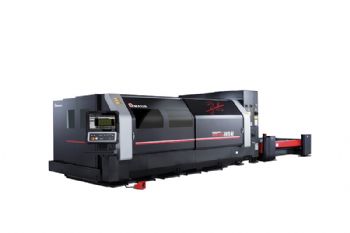
The new Ventis-3015AJ from Kidderminster-based Amada UK Ltd (
www.amada.co.uk) is the first fibre laser cutting machine to feature the company’s LBC (Locus Beam Control) technology, which improves both processing quality and productivity in stainless steel and aluminium.
In combination with a newly developed ‘high brightness’ single-diode-module 4kW fibre-laser oscillator, LBC technology is said to set “a new world standard for laser profiling”.
In conventional fibre laser cutting systems, the energy density declines as the material thickness increases, leading to a lack of efficiency and the need to ‘de-focus’ the beam.
The LBC technology offers flexible beam pattern control matched to each application, while retaining high-efficiency cutting and high energy density; this obviates the need to de-focus, by creating an infinite number of locus patterns.”
The Ventis-3015AJ with LBC technology has three primary modes: Productivity mode, Quality mode and Kerf-Control mode.
In Productivity mode, users can achieve a significant improvement in throughput when cutting stainless steel and aluminium with nitrogen; it will be twice as fast as a conventional 4kW fibre laser when cutting stainless steel and two- or three-times faster when cutting aluminium; and in conjunction with its lower energy consumption, this machine can reduce processing costs by up to 75% in some instances.
Quality mode reduces surface roughness by about 50% and dross to less than 10μm. Indeed, recent trials at Amada’s facility in Japan showed 15mm stainless steel to be dross-free after cutting, eliminating secondary operations such as deburring and reducing processing costs; and even though operating in Quality mode, the trial was run at a cutting speed faster than a standard 4kW fibre laser cutting machine.
Meanwhile, the Kerf-Control mode enables long-term stable processing during automated system operation by controlling the kerf width for optimal efficiency, based on the material type and thickness being processed.
This means that laser cutting shops will not have to struggle with components stuck in the sheet because the part picker cannot deal with a narrow kerf width.
The Ventis-3015AJ has axis travels of 3,070 x 1,550 x 100mm and features the company’s proprietary AMNC 3i control. While the most notable gains from the integrated LBC technology are available on stainless steel up to 20mm thick and aluminium up to 18mm thick, other materials can also be processed — including mild steel (up to 25mm), brass (10mm) and copper (8mm).