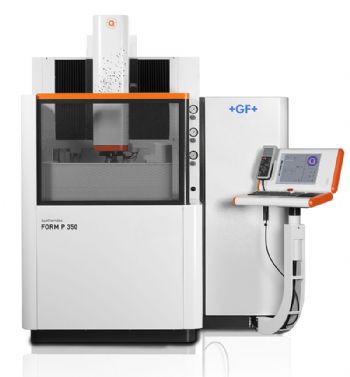
The Form P 350 die-sinking EDM machine from Coventry-based GF Machining Solutions Ltd (
www.gfms.com/uk) features “precision-enhancing qualities and integrated technologies” designed to enhance productivity and profitability.
It has a compact C-axis construction, a fixed table and a cast-iron frame that offer the levels of stability and force reduction required to maintain a precise spark gap between the part and electrode.
GFMS says that — regardless of part weight or dielectric volume — the machine delivers consistently high accuracies and surface finishes of Ra0.1um.
Furthermore, integrated glass scales ensure repeatability and eliminate errors due to backlash and wear, as well as the need for recalibration.
The Form P 350 is equipped with the company’s ‘intelligent power generator’ and Tecform module, which optimises each pulse to reduce electrode wear and produce high-quality surface finishes.
Furthermore, ‘segment-dedicated’ technology eliminates the need to adjust the generator’s parameters, thereby ensuring reliability, improved operational efficiency and reduced unproductive time.
In addition, the company’s IQ (Innovation and Quality) technologies control the erosion of graphite and copper electrodes and help to reduce costs.
The console’s AC Form human-machine interface is Windows-based and provides interactive graphics to illustrate operations such as measurement and machining cycles.
The machine is supplied with a four-position linear tool changer for System 3R macro tooling, and an optional rotary tool changer can be specified; this increases the number of electrodes to 160.
Machines can also be paired with the System 3R WorkPartner 1+ robot for unattended night and weekend operations. The X-, Y- and Z-axis travels are 350, 250 and 300mm respectively, and workpieces up to 700 x 460 x 275mm can be accommodated.