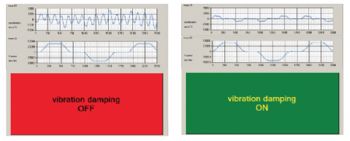
Coventry-based NUM (UK) Ltd (
www.num.com) has launched an accelerometer-based active vibration control system for CNC machine tools.
Primarily designed to improve machining by “virtually eliminating tool head vibration”, the system also increases productivity by maximising the material removal rate; it can also provide valuable real-time feedback for predictive maintenance purposes.
It is available as a retrofittable option for any machine tool that uses NUM’s MDLUX high-performance digital servo drives, which are part of the company’s Flexium+ CNC platform.
NUM says most accelerometers are only capable of low-frequency sampling rates and require additional signal conditioning electronics before they can be connected (usually via Fieldbus) to the CNC or PLC system.
Typically, acceleration data can only be retrieved once every 20 milliseconds, which is inadequate for vibration damping purposes on machine tools; the accelerometer in NUM’s new system is sampled every 100 microseconds, so it can be used for closed-loop control at bandwidths approaching several hundreds of Hz.
The small flange-mounting accelerometer transducer can easily be attached to the machine’s ‘tool head’ and has a sensitivity of 0.02g (1.96m/sec
2), with a measurement range of ±2g (±19.6m/sec
2); and because the transducer connects directly to the digital servo drive, there is no need for any additional signal-conditioning circuitry.
The active vibration control system uses the drive-embedded macros (DEM-X) option that is available on NUM’s MDLUX high-performance digital servo drives.
This allows real-time macros to be embedded within the drive in order to ‘manipulate its regulation algorithms’.
The
output signal from the accelerometer transducer can thus be used to directly influence the behaviour of the speed servo control loop.
All MDLUX servo drive modules use DSP control techniques to maximise the CNC kernel-to-drive servo bus speed; they also feature high loop bandwidths and special acceleration algorithms for optimum speed and positioning accuracy.
A particular application of NUM’s new active vibration control system relates to Tool Centre Point (TCP) vibration due to the various vibration modes of a machine tool’s mechanical structure.
Until now, even if a machine is equipped with a high-resolution encoder (integrated in the servo motor), it has not been possible to damp the TCP vibration, simply because it is not measured.
With NUM’s new system to measure and dynamically alter the TCP acceleration in each of the main axis directions (X, Y and Z), it is now possible to damp the vibration very accurately.