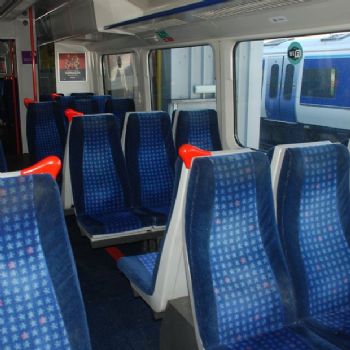
Angel Trains (one of Britain’s leading train-leasing companies), 3-D printing company Stratasys, engineering consultancy DB ESG and train operator Chiltern Railways have joined forces to trial the first 3-D printed parts ever deployed within an in-service passenger train in the UK.
These parts include four passenger arm-rests and seven grab handles.
The aim is to demonstrate how 3-D printing can help train operators to get vehicles back into service quicker
and better maintain their trains.
The cross-industry collaboration aims to “leverage 3-D printing to help overcome issues around the replacement of obsolete parts across the UK rail industry”.
Unlike the automotive industry, where vehicles from household brands are mass-produced in their millions each year, the number of fleets in the rail industry is comparatively small, and some of them are over 30 years old.
This presents several challenges for train operators, especially when it comes to vehicle maintenance and part replacement.
James Brown, data and performance engineer at Angel Trains, said: “In recent times, we have seen growing concern among operators that sourcing replacement parts for older train fleets at a reasonable cost and in a short timeframe is proving increasingly difficult.
“We have teamed up with DB ESG and Stratasys to show how train operators can overcome these hurdles by using 3-D printing to produce the exact amount of parts they need — at a fraction of the cost and in far less time than traditional methods.”
Mr Brown said that the lead time for the arm-rest feature currently in service with Chiltern Railways would be about four months using conventional manufacturing methods, but the final arm-rest can be available within one week with Stratasys FDM 3-D printing — and at a cost saving of some 50%.
In the case of the grab handle, the replacement part was obsolete, and the original supplier was no longer in business.
To make more of these parts conventionally, a new manufacturing tool would have been required — at a cost of about £15,000 and with a production lead time of two and a half months.
With 3-D printing, the seven grab handles required were produced at a very competitive cost within three weeks.