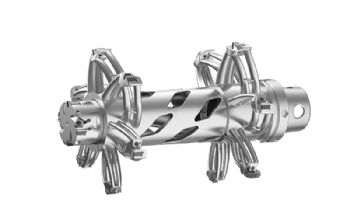
Tooling company Kennametal (
www.kennametal.com) has developed a 3-D printed ‘stator bore’ tool specifically designed to meet growing demand for lighter-weight tooling solutions used to machine components for hybrid and electric vehicles.
The company says e-mobility components are typically machined on compact low-power CNC machining centres, adding that its 3-D printed stator bore tool weighs half that of the conventionally manufactured version — while still meeting accuracy, roundness, and surface finish requirements for aluminium motor body boring.
Harald Bruetting, manager (program engineering), said: “The main bore housing the stator of an electric motor is about 250mm in diameter and some 400mm long; it also has a smaller bore at the bottom.
“When manufactured using conventional means, a ‘reamer’ for this type of application would weigh more than 25kg; this is far too heavy for the existing machine tool — and for the operator working with the tool.”
Mr Bruetting and Kennametal’s Solution Engineering Group turned to the company’s in-house additive manufacturing capabilities to 3-D print a strong but lightweight indexable tool, equipped with proven Kennametal technologies, including fine adjustable RIQ reaming inserts for high-precision finishing and a KM4X adaptor for maximum rigidity.
The tool also features internal 3-D printed cooling channels that help to maximise productivity and tool life.
Werner Penkert, manager (Future Solutions), said: “By using metal powder-bed 3-D printing together with finite-element analysis software, we were able to design and build a tool that brought the moment of inertia very close to the spindle face, increasing its rigidity while meeting the customer’s weight restrictions.
“This is an excellent example of how Kennametal is using advanced manufacturing technology to help meet our customers’ unique challenges.”
Two versions of the tool were built, one with a carbon-fibre tube, the other using a 3-D printed metal tube. The carbon-fibre version weighed 9.5kg, while the one with the printed tube weighed 10.7kg — both less than half of their conventional counterparts.