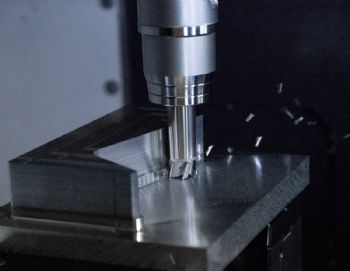
Whether manufactured using traditional processes or additive technology, Ceratizit’s (
www.ceratizit.com) new range of PCD tools has been designed ‘to deliver maximum efficiency’ when processing non-ferrous metals and fibre-reinforced plastics, ‘such is the inherent hardness of this synthetic poly-crystalline diamond cutting material’.
Ceratizit says that with the development of additive manufacturing processes, cutter geometries that were difficult — or even impossible — to produce with conventional technologies are now a reality.
Indeed, the company says that the number of cutting edges on a milling cutter can be maximised with 3-D printing, which in turn significantly increases the chip-removal rate.
This fact, along with high cutting speeds and strategically placed coolant channels, delivers major benefits in terms of reduced cycle times.
Machining performance is also enhanced by high helix angles that ensure quiet running at high spindle speeds.
Screw-in PCD cutters from Ceratizit are available in diameters from 10 to 32mm, with flute lengths of 2.5¥D (tool length can be varied by the use of appropriate tool-holders).
PCD milling cutters can also be supplied in ‘hybrid form’ with a solid-carbide base body.
For companies that are machining graphite, the new Ceratizit PCD tools offer up to four cutting edges and can be run at ‘very high cutting speeds’; and when circular milling holes or grooves, Ceratizit says that many fewer radius corrections are required before the end of the tool life (when compared to solid-carbide tools).