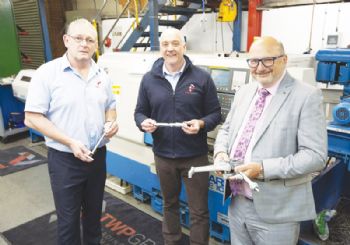
Tipton-based TWP Manufacturing, a high-quality presswork and injection moulding specialist, has set about reshoring a major part of its production process.
For many years, the company has had turned parts manufactured in Singapore, but after a significant six-figure investment advised by Crowe UK, it has purchased six CNC machines to undertake the work in-house.
The project has already been such a success that the directors are ordering a seventh CNC machine for the new year, and three new jobs have been created so far (
www.twpmanufacturing.madeinthemidlands.com).
Established in 1995, TWP provides pressings, mouldings and assemblies to a wide range of UK industry sectors, including automotive, construction, electrical and white goods through to high-profile leisure and retail brands.
Johnathan Dudley, Crowe’s national head of manufacturing, said: “TWP had reached a point where it wanted to take back control of costs and bring the margin back in-house in order to maintain its competitive edge.”
The company has installed three Dugard Eagle CNC machines, a Mori Seiki SH25, an Econo CNC 25 and a Bridgeport 760 vertical machining centre.
TWP director Phil Stanley explained that the company had recognised the need to take more control of processes, batch numbers and lead times, and the best solution was to bring many of the processes back in-house, resulting in the recent investments made in machinery, people and training.
He said: “We are constantly seeking to be more proactive in our relationships with our customers. To that end, we need to be constantly innovating and looking at what we can do better, faster and more competitively in a fast-changing market-place.”