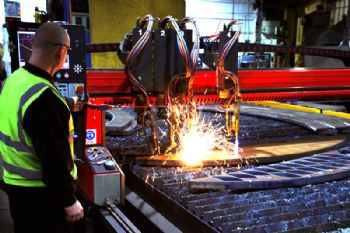
Batley-based PP Profiles (West Yorkshire) Ltd has invested in a 39m-long plasma and flame cutting machine cell — supplied by Rochdale-based Kerf Developments (
www.kerfdevelop ments.com).
Established 43 years ago, the sub-contract manufacturer has built a reputation for providing cutting solutions for customers in the nuclear, oil and gas, construction, rail, bulk handling, food, water and waste, storage tank and yellow goods industries.
The business, which employs 40 people, processes an average of 400 to 500 tonnes of steel every month.
Almost 40% of this material is now run through the new Kerf RUR4500, which has replaced two older 12 ¥ 2.5m flame cutting machines and a 6m plasma machine.
Commercial director Daniel Morley said: “We specified the Kerf RUR4500 with a single high-definition plasma cutting head on a 12 x 4m bed and a two-machine 24 x 4m bed that consists of both a six-head and a four-head flame cutting gantry — all in a single 39 x 4m cell. This allows us to load much larger jobs, and it has opened up new markets.
“The Kerf machine instantly eradicated the need for a late shift and a night shift; we now only work a day shift, with four people running the three machines in the RUR4500 cell.
"We can cut steel plates on the extremely large bed, and while this process is on-going, the crane operator can load the next plate, so as soon as the machine has cut one plate, it can move on to the next.
"This eliminates non-cutting times and slashes set-up times.
“As the new plasma head is running on a 12m bed compared to the previous 6m bed, the benefits of pendulum loading and unloading are particularly pertinent.
“The Kerf RUR4500 has streamlined our workflow, improved our machine utilisation and up-time by 50% and improved our productivity by over 20%.”