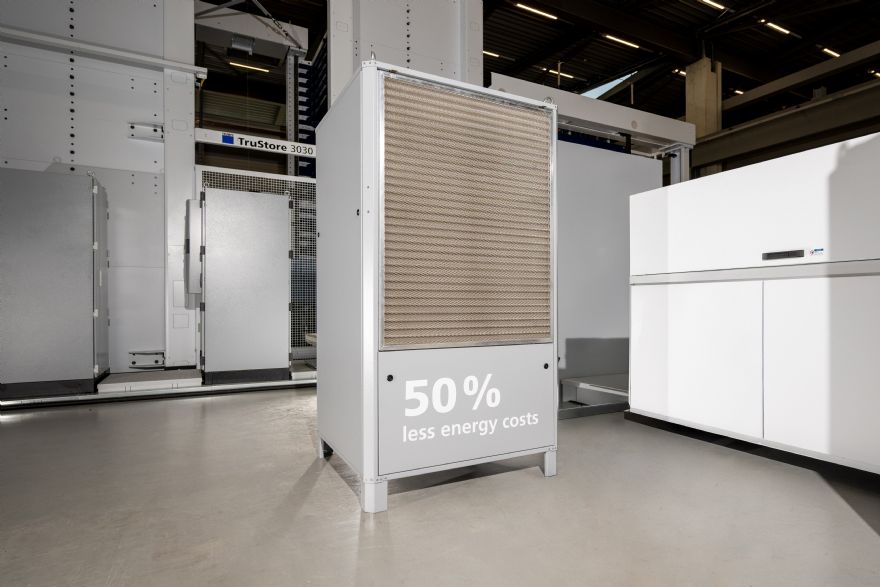
At its forthcoming in-house exhibition
INTECH, taking place this week (1-4 April) in Ditzingend, Germany, high-tech company
Trumpf will be showcasing a new cooler for its laser cutting machines which is capable of reducing energy consumed during the cooling process and uses 50% less energy than conventional solutions.
Unlike conventional coolers, the main components of this new solution — such as pumps, fans and compressors — are equipped with a rotational speed controller. This enables the solution to use only the amount of energy actually required to cool the laser, allowing for a great deal of energy to be saved, particularly when cutting thin sheet metal or during planned breaks in processing.
Fabian Staib, Trumpf’s product manager, said: “With the energy-efficient cooling unit, Trumpf is continuing to make sustainability advancements in industrial production. Users not only save electricity and CO
2 — they also reduce energy costs in the process. This helps companies to remain competitive.”
Due to its high energy savings, the energy-efficient cooling unit pays for itself in less than four years. With a surface area of just 1m
2, the cooler unit easily fits into any production environment. Trumpf currently offers the solution for its laser cutting machines with 24kW laser power. In the future, cooling units will be available for other laser power levels.
With this new cooling unit, Trumpf is helping sheet metal processing companies reduce their consumption of coolants in-line with the Kigali Amendment, a 2016 agreement stipulating the global phase-out of environmentally harmful refrigerants. The cooler’s refrigerant — R513a — has a significantly lower global warming potential and thus meets the Kigali Amendment’s stricter regulations.