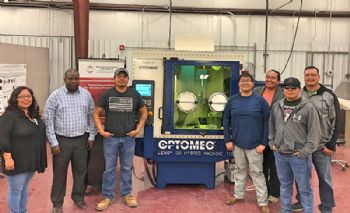
New Mexico-based Optomec (
www.optomec.com) — a privately owned global supplier of production-grade additive manufacturing equipment and software — has confirmed that its LENS Directed Energy Deposition (DED) 3-D printed metal system will be used to print bi-metallic rocket engine parts “that will go to the moon in 2024, thanks to a grant from NASA for additive-manufacturing research and education”.
The grant has led to collaboration between the Navajo Technical University (NTU), the Marshall Space Flight Center’s Advanced Manufacturing Center, the University of Alabama Huntsville, V&M Global Solutions and Optomec.
They will work together on additive-manufacturing research around the DED of bi-metallic parts for NASA applications and build institutional capacity in STEM research and education.
Tom Cobbs, Optomec LENS product manager, said: “We are very excited to be working with this team and NASA to explore how the benefits of additive manufacturing can be applied to space exploration.
"LENS is an ideal solution for printing multi-material components used in higher-performance liquid rocket engine components; it has the potential to provide significant advantages in terms of cost and time savings, especially if we can print the bi-metallic parts on one machine in one process.”
The proposed research will focus on characterisation (micro and nano-scale) of the microstructure of AM Inconel-Cu alloy bi-metallic parts in three conditions — as built; during hot-isostatic pressing and heat treatment; and after hot-isostatic pressing and heat treatment — in order to establish the linkages between microstructure, post-processing, dimensional accuracy and mechanical properties.
The research will also involve metrology to provide insights into the dimensional accuracy of DED printed parts for use in the Space Launch System.