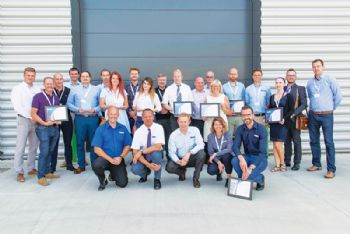
Digitalisation is fuelling consumer demand for product customisation. Responding to this, Surrey-based Broanmain Plastics (
www.broanmainplastics.co.uk) has launched a new precision-moulding/manufacturing facility that caters to branded customised precision components used in the automotive, aerospace, electronics and fast-moving consumer goods sectors.
To repeatedly achieve a better surface finish on parts featuring intricate 2-D and 3-D geometries, the company has invested in ‘state of the art’ vertical CNC milling technology at its Dorking manufacturing facility.
At
Southern Manufacturing 2020 (Stand C195), visitors will be able to see — and handle — real examples of customised industrial devices engineered and made for blue chip multi-nationals, including one of the world’s largest suppliers of life sciences instruments.
Broanmain’s milling facility can manufacture intricate parts from a range of materials, and it enables the company to repair and prototype customers’ mould tools in-house.
Another new addition to its tool shop is a ZNC spark eroder.
This enables its CNC machinist team to make precise shapes and forms in hardened and conductive materials that could not be accomplished using a manual or CNC milling machine.
Managing director Jo Davis said: “For OEMs seeking bespoke moulded and fabricated parts — all managed through a single supplier — Broanmain has the flexibility, tools, production and assembly resources to undertake manufacturing and prototype projects of all shapes and sizes.
“We also project-manage tooling commissions. This expertise helps to de-risk projects, especially in the early development phase.”
In the last 12 months, Broanmain has added eight more machines to its injection moulding capability; its higher-tonnage machines can mass-produce components weighing up to 3kg.
The company also reports an unprecedented rise in demand for compression moulding, which Ms Davis attributes to the reduction in UK moulders offering both injection and compression moulding.
“Many suppliers are simply not training new staff in this older technology, so there are fewer moulders with the capacity or resources to meet customers’ delivery demands.
“We have increased the capacity of our compression moulding department, and we are focused on developing more team members to support this growth.”