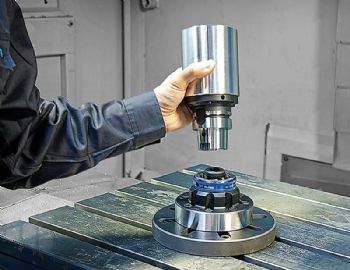
Salisbury-based 1st Machine Tool Accessories Ltd (
www.1mta.com) will debut the new Kitagawa Swift Klamp (pictured) in the UK at
Southern Manufacturing 2020 (Stand G205).
This is a rigid work-holding product that uses the proven HSK tool interface to provide a low-interference quick-change clamping arrangement that resists the bending forces generated during metal-cutting operations.
Designed for five-axis machines, it is equally suitable for use on three- and four-axis machines.
The clamping head is supplied either as a manually or an automatically operated HSK clamp, while the work-holder comprises an HSK interface at the base and one of multiple options at the top for holding the workpiece, including flange clamps and side clamps.
The most-efficient clamping system is the dovetail interface, which requires a slot to be pre-milled into the raw billet to match the holder profile (a solid-carbide cutter is available specifically for this purpose).
The small clamping surface area allows enhanced tool access, and its low profile maximises the machine tool’s Z-axis travel.
Workpieces up to 200mm square or diameter can be accommodated.
Additionally, pre-machined dovetailed steel and aluminium blanks can be supplied in various sizes for immediate use.
The manual clamping head has a versatile flange that suits multiple mounting options.
Available in HSK-A40, HSK-A63 and HSK-A100 sizes, it can be set up off-line, and the work-holder can be exchanged within 10sec, minimising machine down-time.
For automated manufacturing processes, a hydraulically actuated clamping head is available in the same HSK sizes, with seating detection and air-blow.
The work-holders have a standard profile to enable them to be handled by any general-purpose robot arm.
Also on demonstration at
Southern Manufacturing will be the new RotaVice workpiece-positioning system, which is suitable for production shops where manual mills may still be in operation but also suitable for use on a vertical machining centres.
It is a manually adjustable indexing head that can be rapidly set to position a component at a multiplicity of rotary angles in the horizontal plane for milling and drilling.
Produced in the UK, it is designed to be secured in a One-Lok work-holding device manufactured by Chick in the USA, for which 1st MTA is the sole agent in the UK and Ireland.
RotaVice can also be exported to manufacturers world-wide that use similar Chick equipment.
Everything about the RotaVice is fast.
First, a One-Lok can quickly be bolted onto a VMC table.
Next, positioning the moveable jaw using the built-in time-saving ratchet mechanism leaves only a few turns of the handle to clamp the indexing head in a special RotaVice jaw (made by 1st MTA) that replaces the standard One-Lok jaw.
Lastly, the workpiece is secured in moments in a horizontal orientation using an array of work-holding options, which include a three-jaw chuck.
Adjusting the angle is also rapid and accurate.
It is effected by turning a circular locating plate to the required angle and inserting a pin into the relevant hole (one of a number pre-drilled into the plate at the most common angles).
In the standard configuration, 5, 10 and 45deg are available; the standard plate can be changed for a specific plate to suit any job that involves the use of non-standard angles.
Another advantage of the RotaVice is that once the angle has been selected, it uses the clamping force of the One-Lok to secure the rotary angle.
This force, which is much higher than that offered by standard dividing heads, allows significantly heavier machining cuts to be taken and delivers an improved surface finish.
Altering the angle for a subsequent machining operation on the same component is similarly achieved without having to re-clamp the part, thereby avoiding loss of accuracy through tolerance build-up.
Intermediate angles can be set using a rotary dial with a 1deg increment scale, while very fine adjustments down to ±0.5deg can be made using the toggle lever mounted at the top of the unit.
Importantly, RotaVice has a large through bore with a taper and an internal thread, both of which can be configured for use with chucks, mandrels, special fixtures and back-stops.
These are normally not associated with standard dividing head systems.