Expansion includes three-machine fibre laser cell
Posted on 17 Feb 2020. Edited by: John Hunter. Read 2904 times.
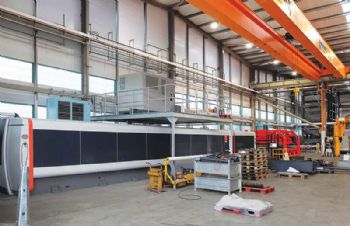
The Irish sheet-metal fabrication and CNC machining sub-contractor Inishowen Engineering, which recently celebrated its 25th anniversary, has dramatically increased the size of its production facility in County Donegal, following an
11 million euro investment in a new 160,000ft
factory that opened on the company’s seven-acre site in Drumfries in early 2019.
As part of the expansion programme, which started in April 2017, an extra 19 million euros has been spent on new machine tools, a pair of robotic welding stations, and new finishing equipment; the latter includes shot-blasting booths, wet and powder painting lines, and a nano pre-treatment and electrophoretic coating facility. I
n addition to replacing a CNC tube bender and a plasma cutting machine with more-modern plant and the purchase of another large machining centre, other new machines on site include a 12 x 2m-capacity 6kW flat-bed fibre laser cutting centre; this joined two 4 x 2m-capacity models of similar power installed earlier (in 2015 and 2017).
All three are BySprint Fiber Laser machines manufactured by Bystronic in Switzerland and supplied by Coventry-based Bystronic UK Ltd (www.bystronic.com).
Also on site from Bystronic are seven press brakes, as well as a machine with a CO2 laser for cutting tube up to 305mm in diameter x 12,500mm long; and during the spring of 2019, the company supplied and installed an automated sheet storage and handling system that continually loads and unloads material to and from the three flat-bed lasers, reducing the manning requirements on these machines and improving productivity.
Michael McKinney, owner and managing director of Inishowen Engineering, said: “Underlying this latest round of investment is our diversification from concentrating mainly on the agricultural, quarrying and mining sectors
to supplying firms manufacturing materials-handling and transportation equipment, including fork-lift trucks and multi-purpose tractors.
In all of the industries we serve, the component parts and assemblies we are asked to produce are becoming larger, so that customers can minimise welding when manufacturing their products — hence the need for machines capable of processing 12m-long sheet and tube.”
Increased capability
In the case of the tube laser cutting machine in particular, which was delivered in the second quarter of 2019, Mr McKinney said this new offering to customers sets the company apart from most sub-contractors in Ireland — and in the UK — by broadening the company’s capability considerably and preventing work being lost to competitors.
“The tube laser can complete in 5min what might take 4hr of manual milling and drilling on different metal-cutting machine tools.
"Moreover, some components cannot be produced at all by conventional means, so OEMs’ now have greater design freedom, knowing that more-complex parts can be produced — and at an economical price.”
Regarding the Bystronic handling system, which comprises two 10m-high storage towers with 82 locations for 4 x 2m sheet, together with loading and unloading equipment for the three fibre lasers, Mr McKinney said that formerly the only reason for the machines being idle was due to material not being fed to them quickly enough.
“Now that sheet supply has been automated, it is delivered much faster to the shuttle tables, enabling virtually uninterrupted production. We estimate that output from the two smaller machines is up by 30-50%.
“Previously, we were perpetually 400-500hr behind with laser cutting, but within three weeks of the lasers being supplied with sheet from the Bystronic storage system, the backlog had disappeared.
"A further advantage of automatic material feeding is that it is now easier to promote rush jobs to the top of the queue.”
Inishowen Engineering’s two smaller fibre laser cutting machines replaced models with 6kW CO2 power sources; these were installed in 2007 and 2010.
Mr McKinney says that fibre technology is five-times more productive than CO2 when processing 2mm mild steel, cutting
at 40m/min.
He adds that the advantage declines somewhat as sheet thickness increases (12mm material is cut regularly), “but the sheer speed of the fibre machines across all gauges only serves to underline the need for efficient, automated delivery of material to the point of cutting.
Moreover, the BySprint Fibers not only cut significantly faster but also cost less to service and run, as there are no optics or need for assist gas — and electricity consumption is much lower.
"Furthermore, their greater reliability means that we are confident leaving the machines running unattended overnight.”
The increasing size of components going through the factory necessitated a press braking cell to bend parts up to 12m long — hence the installation at the start of 2019 of two Bystronic Xpert 6m x 650-tonne capacity press brakes.
These are positioned side by side, so that they can be used individually or in tandem, mirroring an earlier purchase of a pair of 4m x 400-tonne press brakes.
However, because half of all profiled sheet that is folded in the factory is less than 1m long, in 2015 Mr McKinney bought an Xpert 40 1m x 40-tonne-capacity press brake.
He says this is not only at least one-third faster at bending smaller components than larger machines but also draws considerably less power — just 7.5kW instead of typically 30kW for a big press brake.
The Xpert 40 was so successful in raising the profitability of smaller component production that two years later the folding department added the next model up in the Xpert range — one with a 1.5m x 80-tonne capacity.
Summarising the latest phase of his business expansion programme, which is just coming to fruition, Mr McKinney concluded: “There is a trend towards OEMs downsizing their in-house manufacturing, reducing their capacity and out-sourcing more assembly operations in order to cut costs.
"However, for sub-contractors to win this business, they need to invest in the best and most modern production equipment to satisfy customer demand and expectation.
"That is why we have standardised on Bystronic laser cutting and folding machines since buying our first CO2 BySprint in 2007.
“Smaller firms may struggle to finance the acquisition of top-end machines, but only by doing so is it possible to obtain high quality coupled with competitive cost-per-part production; and especially when producing assemblies, which account for two-thirds of our throughput, accuracy in all areas of machining is essential to avoid time-consuming fit-up difficulties. The same applies in our customers’ factories.
“Inishowen Engineering’s latest 30 million euro investment allows us to leverage the advantages of high precision combined with competitive pricing. It is a clear statement of our intention to become one of the foremost ‘one-stop shop’ fabricators in Europe.”