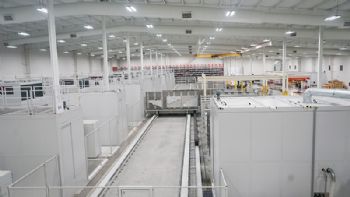
Today, more than half a century after singer Gene Pitney put America’s southern central state of Oklahoma on the world map with his hit song ‘24 hours from Tulsa’, something else is bringing ‘global recognition’ to the area — Orizon Aerostructures.
This manufacturing and technology company, which has six locations and 763 employees dedicated to manufacturing complex aerospace parts and sub-assemblies, operates almost 780,000ft
2 of production area at sites in Kansas and Missouri, as well as Oklahoma; these include four machining locations which between them use 100 CNC machines, 50 of which have five axes or more.
However, it is in Orizon’s newest plant in Grove — a little under a 90min drive from Tulsa — that ‘a new tune in manufacturing excellence is being played’.
The company has installed a flexible manufacturing system (FMS) based around nine five-axis Ecospeed machining centres from Starrag, which has a UK subsidiary in Birmingham (
www.starrag.com).
The FMS — reputed to be ‘the largest integrated system of its type in the western hemisphere’— is enabling Orizon to achieve: at least a 30% reduction in machining times across all parts, compared to former methods; a significant improvement in surface finish, with much less need for subsequent deburring and polishing; and an ‘amazing’ revenue-to-capex ratio, compared with traditional methods of machining.
Commenting on this level of performance, Starrag North America’s managing director, Udo Herbes, said: “That’s no surprise, when it is realised that the Ecospeed can convert a 550kg aluminium billet into a 24kg complex structural part in less than 4hr, when the machine is running at a maximum cutting volume of up to 10,000cm
3/min.”
Minimal manning
The nine high-speed Ecospeed machines (50m/min traverse rates) forming the heart of the FMS are fed by an automated rail-guided pallet system that accesses 18 stations and an integrated washing/drying cell.
The system is manned by just five people on each of the two shifts per day for 24/7 operation and enables Orizon to achieve ''extraordinary machining benefits” on the range of aerostructures — primarily wing spars, skins and bulkheads for leading aerospace and defence OEMs.
Orizon’s forward-thinking machining philosophy is certainly paying dividends, and the company’s attitude towards its investment is clear, as CEO Charlie Newell outlines: “In October 2016, we dreamed of building something unique and building it in just 12 months — a new factory to house an FMS that would produce machining efficiencies to surpass anything we have ever encountered.
“Working from the outset with Starrag, together we have created a highly successful partnership for the world-class machining of aerostructure parts.
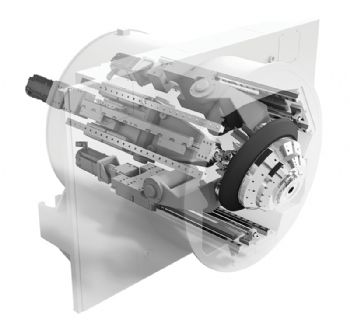
“It was clear, even before the first machine sale, that Starrag was willing to listen and to support our vision by offering excellent levels of knowledge transfer and assisting us to develop the appropriate processes around our business systems.
“These included standardising machining operations, and using standard tooling across all the parts we machine, plus access to online diagnostic tools via Starrag’s Integrated Production System (IPS) that enable Orizon — along with Starrag Technology at Mönchengladbach, Germany — to ‘interrogate’ the system or individual machines via smartphones, iPads or desk-top computers at any time of the day or night.”
Online diagnostics are just one aspect of Starrag’s IPS, a modular digital platform that offers users a ‘suite of functionality to meet individual tasks’.
These include: cloud-based solutions designed to help users analyse and optimise processes to further increase productivity; a system that monitors production in real time and protects the machine against incorrect operation/collisions; in-process quality control with a ‘chatter monitor’ that warns of ‘dangerous vibrations’ when machining; and an integrated machine qualification system that provides information about machine condition and, where necessary, displays the corresponding maintenance instructions.
Verified performance
Orizon president Henry Newell said: “Orizon chose Starrag Ecospeed F2060s, each with a Sprint Z3 parallel kinematic machining head and angular milling head, because we were shown that the machine could achieve everything Starrag said it would.
“This included a metal removal rate of up to 650,000 cubic inches of chips an hour per machine, an uptime of 97%, and excellent surface finishes — courtesy of superb ‘jerk’ speeds.”
However, it was not simply a case of Orizon placing an order for the initial six machines for the FMS (with the plan to add another three machines, and perhaps more in the future).
Orizon first installed a stand-alone Ecospeed with the Z3 head to thoroughly test the machine’s effectiveness and efficiency on production parts.
Orizon’s original Ecospeed F2060 sits alone in its own area, enabling the 86,000ft
factory floor to house the FMS.
The first F2060 was installed in January 2017, followed two months later by the pallet system, and this combination was in production by October 2017.
“A year later, three more Ecospeeds were added. Josh Fink, vice-president of machining, said: “Importantly, these latter three machines did not add any labour overhead to the system — just revenue.”
Starrag’s Ecospeed F2060 has a work envelope of 6,300 x 2,500 x 670mm (spindle in horizontal position). In addition, the ±45deg A/B axis is complemented by a 120kW 30,000rev/min spindle (83Nm of torque) that can run continuously at 30,000rev/min in S1 mode.
The specification is additionally enhanced on a machine with high dynamics in acceleration (up to 1g in all five axes) and ‘jerk’ of up to 200m/sec3.
The load/unload station sees the parts (up to 12 different parts per pallet, although workpiece size — especially heights — are standardised on each 2 x 6m pallet, which can accommodate loads of 5,000kg) loaded manually and secured by a mixture of vacuum and mechanical clamps, with the pallet in the horizontal position.
Once loaded, the pallet is tilted 90deg and is moved into the 270ft-long FMS.
An advanced cell controller ‘decides’ which machine will process which pallet; and with common tooling held by each machine’s 129-station tool-changer, any F2060 can machine any part in any order.
After machining, pallets move to the wash/dry station, although the use of minimum-quantity lubrication means that workpieces entering this station carry a relatively low amount of swarf/cutting fluid.
Cleaned parts are deburred, then 100% inspected on a CMM.
Parallel kinematics
Each of Orizon’s Ecospeeds features a Sprint Z3 parallel kinematic machining head for “highly dynamic simultaneous five-axis/five-sided milling and drilling”.
The head uses three parallel linear-axis drives that are mounted radially and equally spaced in the headstock.
The spindle moves in a straight line in Z when all three axes move simultaneously, while synchronised motion of the three Z axes allows the spindle to follow any path within a spherical cone of ±45 deg at a maximum speed of 80deg/sec.
If the three axes move differentially, the spindle platform will be tilted in the ‘A/B kinematic’.
Each machine has an integral C axis to allow the use of automatic interchangeable angular milling heads that effectively make each machine a six-axis unit, allowing machining access to otherwise difficult-to-reach areas.
Standard HSK A63/80 taper tooling is used, along with ‘mono tools’ up to 50mm in diameter.
All tools feature RFID chips for effective tool management.
One measure of the collaboration between Orizon and Starrag is the fact that the latest three Ecospeeds installed feature design ‘tweaks’ to meet Orizon’s specific needs; these ‘tweaks’ include modifications to the ‘pedestrian door’, improved lighting for in-machine cameras and an improved access door for maintenance routines.
Orizon operators undertake basic maintenance routines, although these are complemented by Starrag’s Service Plus preventative maintenance scheme (an annual fee covers every eventuality and guarantees service response times, inspection and repair).
Despite having achieved massive gains in machining efficiency, Orizon is not resting on its laurels, as Mr Fink points out: “System performance is continually scrutinised, with conference calls every week between us and Starrag to discuss machine availability levels — currently 97%, with 87% the target for spindle utilisation.”