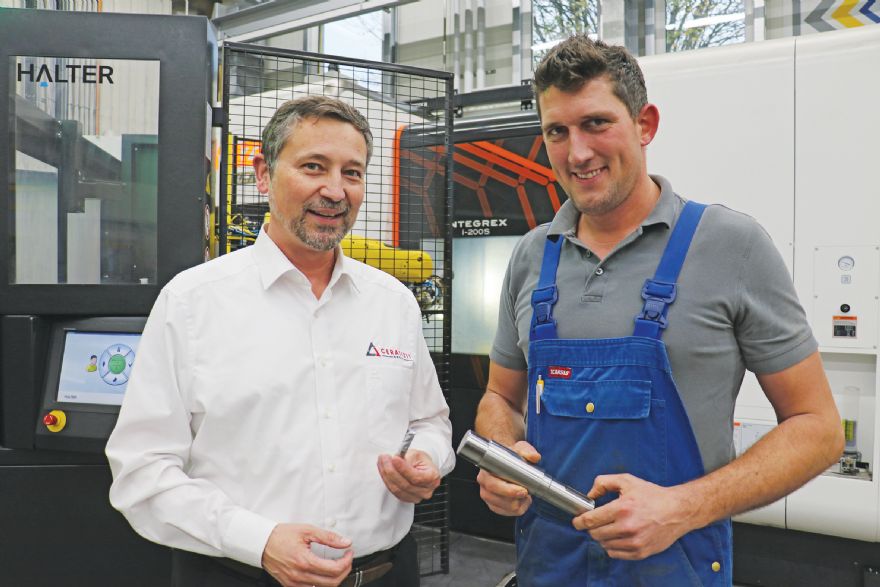
SilverLine has been part of the WNT product range for over 10 years (the company is one of the Ceratizit Group’s ‘competence brands’ —
www.ceratizit.com), so it was time to look again at this key product and update it — not only with the latest in cutting-tool technology but also by expanding its application range with new cutters.
The development team was tasked with improving the three key areas that give a solid-carbide tool its high performance — the carbide substrate, coating and geometry — while also delivering significant improvements in tool life.
Larger core diameterAlong with changes to cutter geometry, the new substrate has resulted in a completely new core to the SilverLine cutters. Increasing the number of flutes allows a larger core diameter to be used, which provides greater cutter rigidity and reduces deflection for increased overall process security (the tensile strength has been increased by 50%). Moreover, changes to the chip gullet and the addition of through-tool coolant further improve chip flow, reduce cutting forces and minimise the amount of heat and noise generated.
The result is that — depending on the material being processed — cutting data can be increased by 20-40%, while tool life increases by as much as 50%. The new cutters also feature Ceratizit’s Dragonskin multi-layer coating; silver in colour, this is compatible with most materials and has a high thermal resistance, enabling it to be used for either wet or dry machining applications.
Adrian Fitts, business development manager ay Ceratizit UK & Ireland Ltd, said: “In short, SilverLine cutters are now stronger, last longer and can run faster than their predecessors. They are available with three, four, five, six or eight flutes, depending on application and diameter; and with the aerospace sector in mind, we have added many more options when it comes to corner radii, cutter diameters and cutter styles — including ripper and torus cutters.
“Indeed, we listened to customers who were asking for heavier-duty roughing cutters; thanks to the increased core size and rigidity, we can now offer a ripper version of SilverLine.
“With the strengthened core, through-tool coolant and Dragonskin coating, combined with a ripper-style geometry to create smaller chips, we can push tools harder, as chip evacuation is no longer the issue it once was.
“We have also added HA-style shanks to the standard range of SilverLine cutters. This plain shank can be used with heat-shrink and hydraulic chucks, and it allows increased spindle speeds to be used.”
Customer applicationTo prove that SilverLine was ‘a good tool made even better’, extensive field trials were undertaken in Germany — including at long-term SilverLine user Heinz Knöpfle GmbH, a family-owned business that has developed from a manufacturer of low-volume parts for its own special-purpose machinery into a high-volume machine shop providing sub-contract capacity for customers in industries such as medical, scientific, aerospace and general engineering.
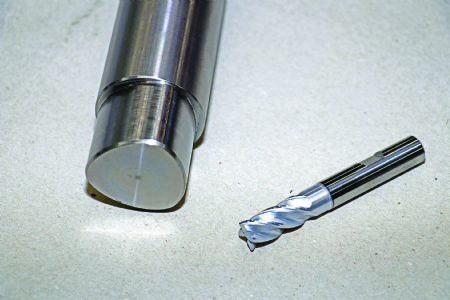
Managing director Susanne Knöpfle said: “We have a raw-materials warehouse containing materials of various sizes and grades, along with a machining capability that allows us to completely machine parts from 10 to 800mm in diameter — and up to 2,000mm long.”
Heinz Knöpfle has 18 Mazak CNC machines, and the Ceratizit Group is the ‘dominant force’ among its cutting-tool suppliers, providing wide-ranging support from its four ‘competence brands’ (Ceratizit, WNT, Komet and Klenk). The new SilverLine tools were tested for six months on most of Heinz Knöpfle’s CNC machines.
Christian Knöpfle, who is in charge of production, said: “As a big fan of the original SilverLine tools, we had very high expectations, but the results we achieved with the upgrade far exceeded our expectations.
“We were able to use cutting speeds that were 20-40% higher, while achieving a service life that was greater by 30-40%; and we noticed straight away that the new SilverLine tools are quieter, thus reducing the burden on the machine.”
SilverLine was initially tested on a ‘challenging’ application — machining a stainless-steel polygon shaft that Heinz Knöpfle produces in various sizes for a water management company.
Christian Knöpfle said: “The SilverLine not only impressed on stainless steels but was also found to be suitable for any application. We use these tools at extremely high cutting speeds while achieving excellent chip evacuation — with a service life and level of process security that other milling cutters do not offer.”